
山一ハガネが誇る世界最高のフィギュアスケートブレード「YS BLADES」。
世界のトップ選手も愛用し絶賛する純“Made in Japan”の金属加工製品だ。
YS BLADES登場前までは、フィギュア選手はスケート靴に様々な課題を持ちながらも、解決の手段がなく半ば諦めており、安定しない品質のブレードに選手が合わせるという“逆転現象”が起きていた。
「選手のブレードに対する悩みを聞いた瞬間、我々ならもっと良いものがつくれると思いました。」
山一ハガネ代表取締役の寺西の言葉だ。
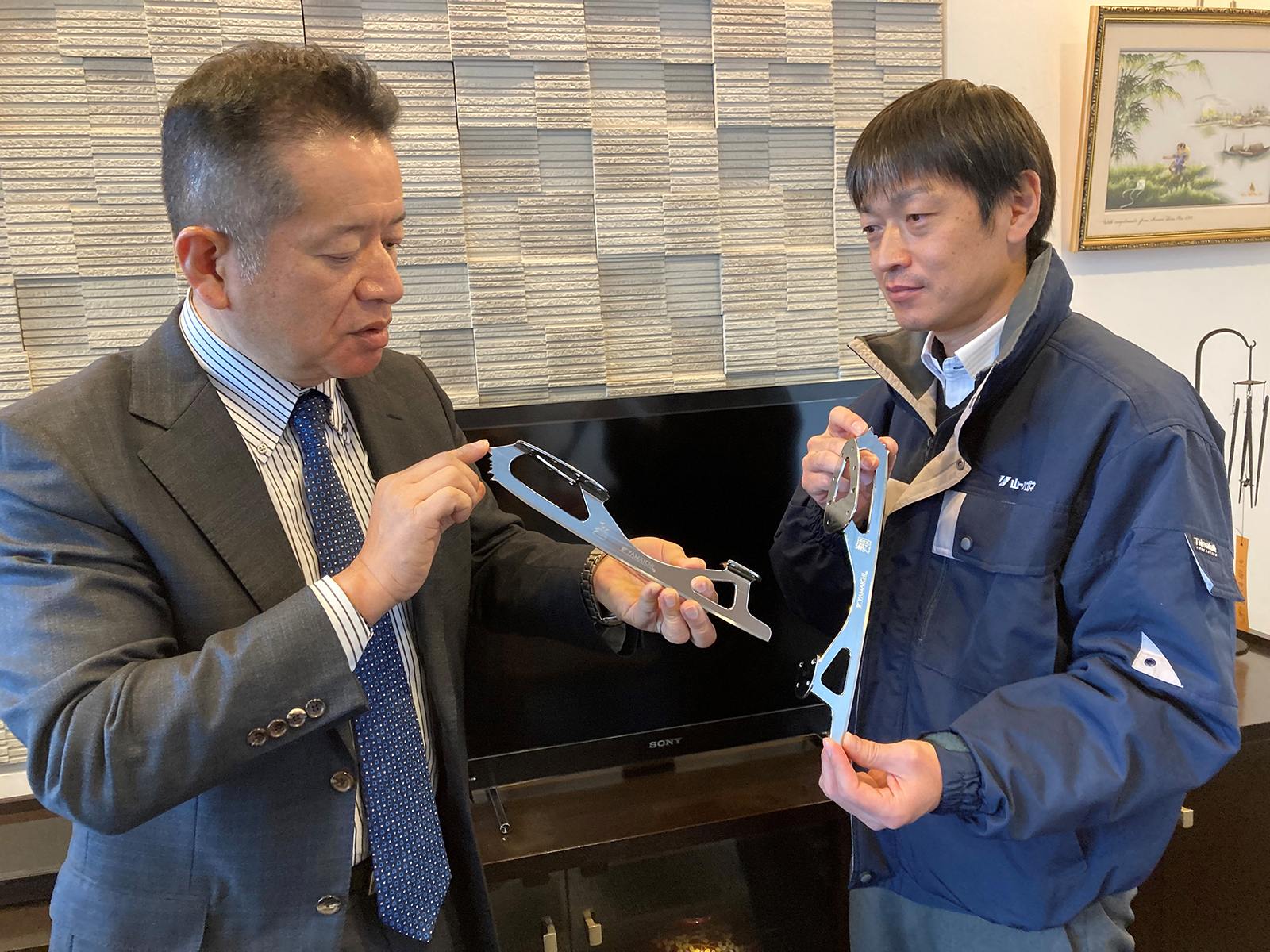
特殊鋼を扱い100年の歴史を持つ山一ハガネが、その知見と技術の粋を結集。「顧客(選手)のお役に立ちたい」という熱い思いでモノづくりに向き合い課題解決に導いた。
選手のスケート靴への思いと現状の問題点から、「課題」つまりは「スケート靴が持つべき必要機能」を明らかにすると、山一ハガネが持つ「材料特性のコントロール技術」や「仕上がり品質を高レベルで確保する加工・測定技術」で課題をすべて解決する事ができた。
また、選手が求める履き心地のフィーリングを同じ“温度感”で感じるために、設計者自らも一緒にスケートリンクに立ち、感覚値である“フィーリング”を“設計値”へと変換し、山一ハガネの製造現場で作り込んでいった。
スケートリンクと製造現場の行き来を繰り返し、150セット以上にも及ぶ試作品の数々は、選手の“フィーリング”を大切にした顧客満足への「熱い思い」の表れである。
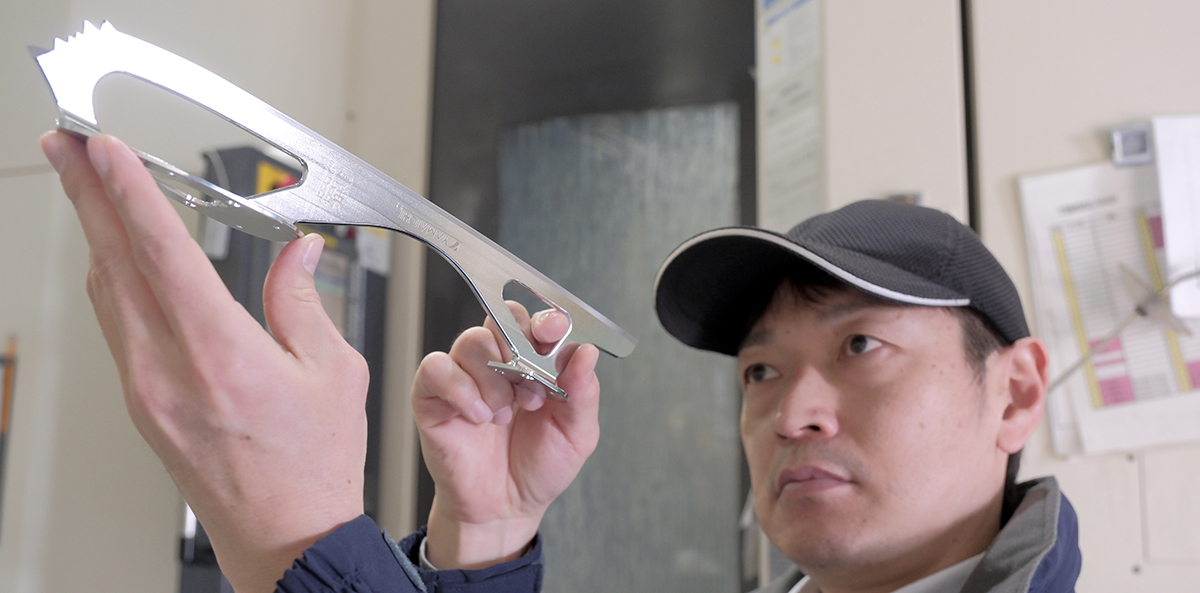
このように、YS BLADESは「たまたま山一ハガネで作れた」のではなく「山一ハガネだからこそ作れた」「山一ハガネでしか作れなかった」製品なのだ。
そんな選手と設計者、技術者の「熱い思い」の詰まったYS BLADESができるまでを、主に技術者の視点からご紹介する。
YS BLADESは製品設計(機能設計)から自社で取り組んだ事例
■YS BLADESの製品設計フロー
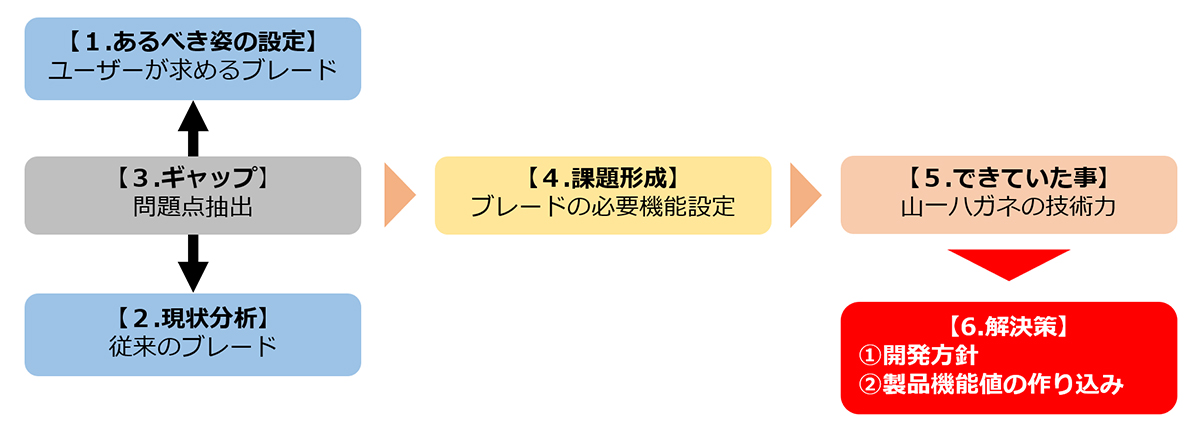
【1.あるべき姿の設定:フィギュアスケート選手が思い描くブレード】
- 4回転半のジャンプを飛んで着地しても剛性が高くて着地感が良い。
- ブレードの寿命が延びることで馴染んだ靴を長く履きたい。
【2.現状分析:従来のブレード作り】
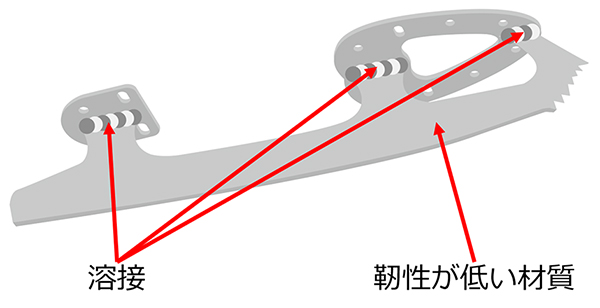
- “溶接”による3ピース構造。
- 靭性が低い材質を使用。
【3.ギャップ:問題点】
- 溶接による継ぎはぎ構造で強度が低い。
- 手作業のため品質にバラつきが発生。
- 素材の“靭性”が低いため、着地時の衝撃により破損・怪我の恐れがある。
- 上記問題点により寿命が短いため、頻繁に交換が必要。
【4.課題形成:ブレードの必要機能設定】
- 溶接のない一体構造により強度向上。
- 手作業を排除し、品質のバラつきがない加工。
- 怪我防止のため、靭性と剛性を兼ね備え、変形と破損リスクを低減。
- メンテナンス回数を大幅低減し長寿命化。
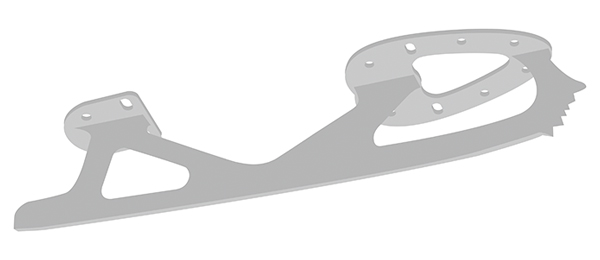
「壊れない」「高品質(安定品質)」「パフォーマンス向上」…選手の「願い」が詰まった「夢」のブレード開発。
【5.できていた事:山一ハガネの技術力】
- 鋼材販売を生業としており、金型材、バネ材の特性の知見が豊富。
- 社内で熱処理設備を持ち、硬さと靭性の調整技術がある。
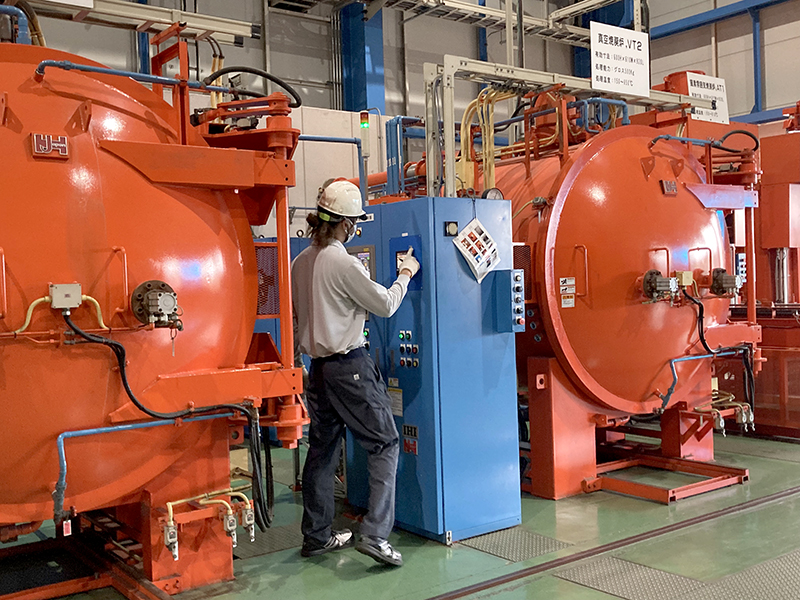
- 10年以上、HERMLEの5軸機、YASDAの高精度機を使いこなし、材質特性に応じた加工ノウハウを持つ。プレス、樹脂、ダイカスト等多種類の金型部品の加工実績がある。
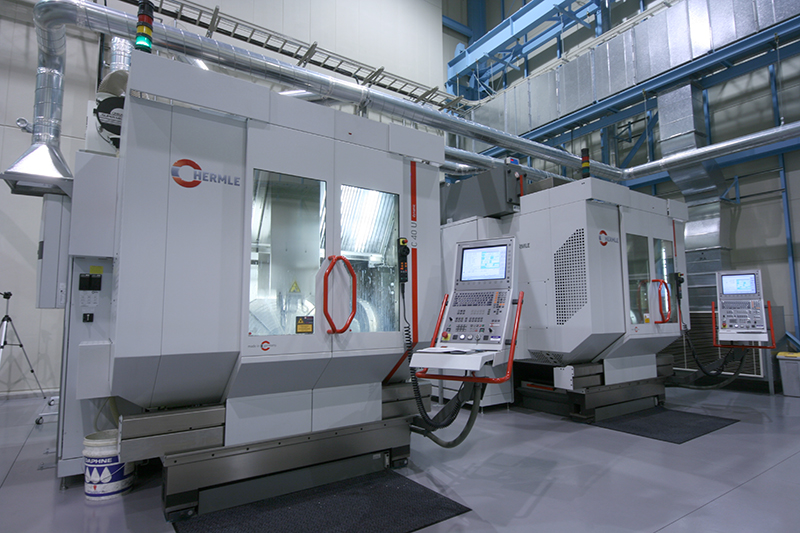
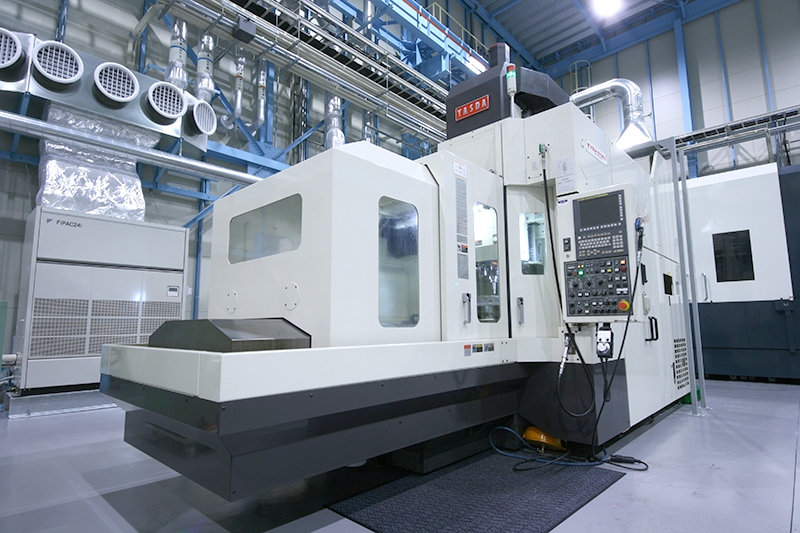
- 加工後の形状・機械特性を必要機能に合わせ込み、維持する加工ノウハウを持つ。
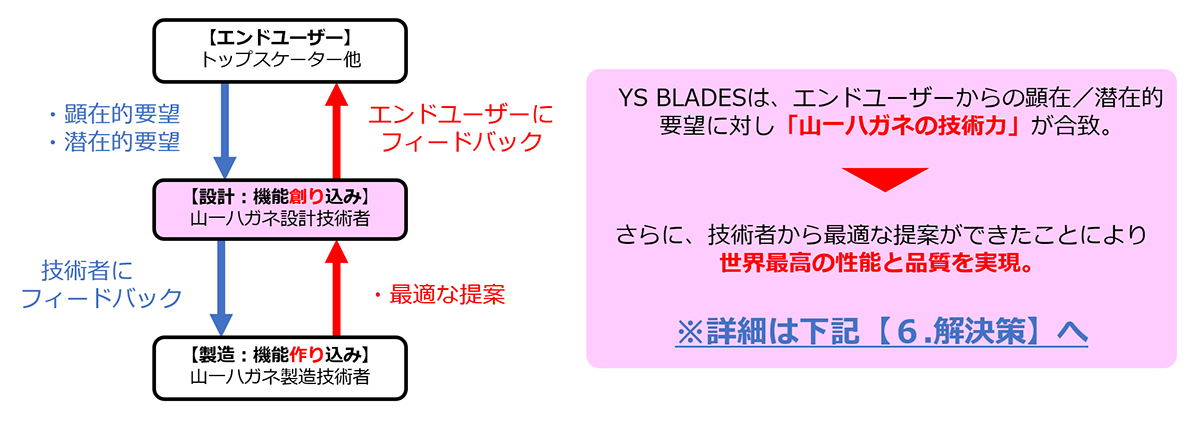
【6.解決策】
①開発方針
<形状設計>
・トップスケーターとの共同開発により基本設計を実施
・基本設計を基に、要望に応じて設計変更
<材料機械特性の最適化>
・社内で扱う特殊鋼約50種類から5種類に絞り込み
・熱処理技術で硬さと靭性を最適化。
<製造方法>
・材料の塊から一体物を削り出し
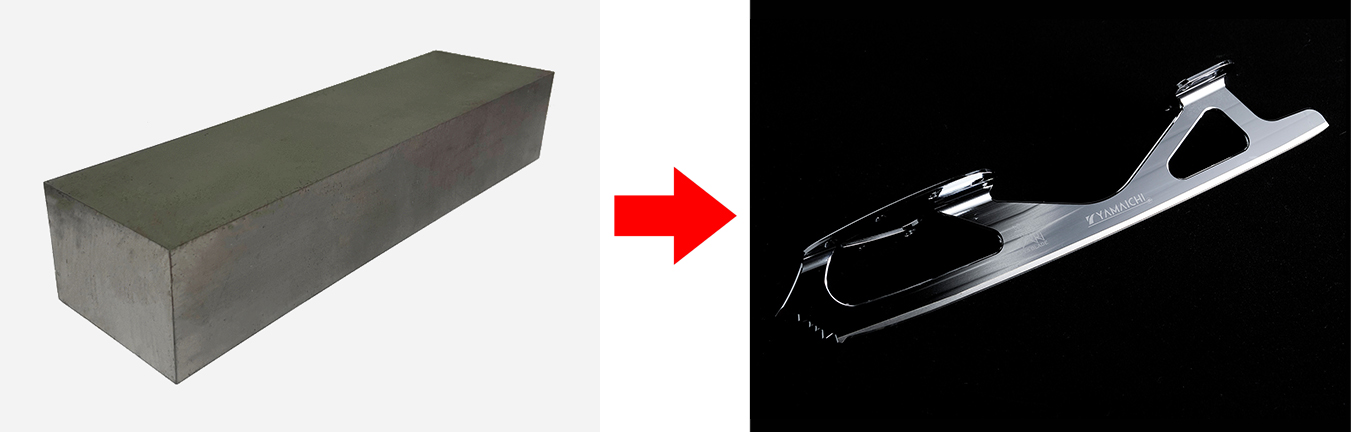
・CADデータからの数値制御加工
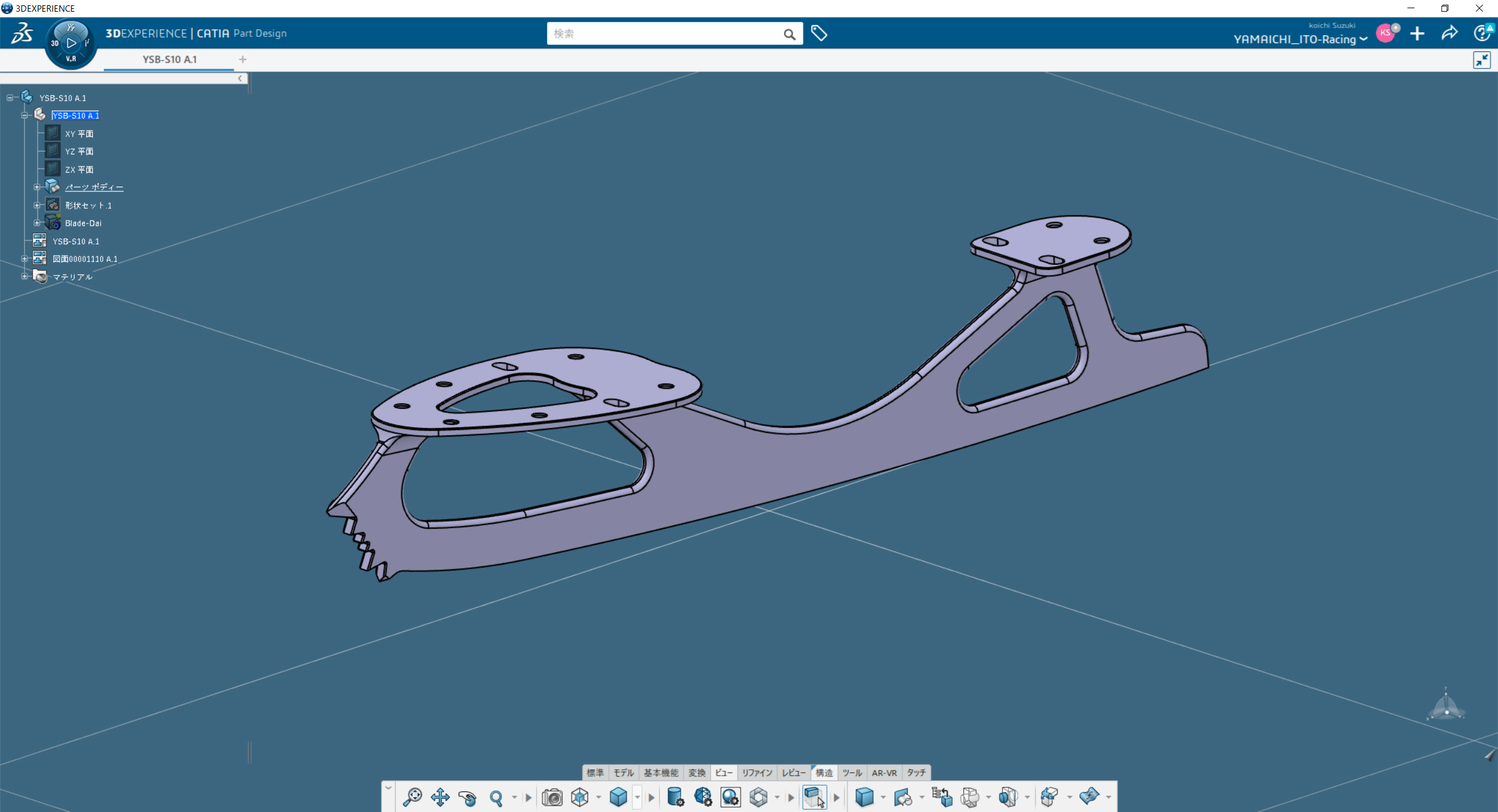
②製品機能値の作り込み
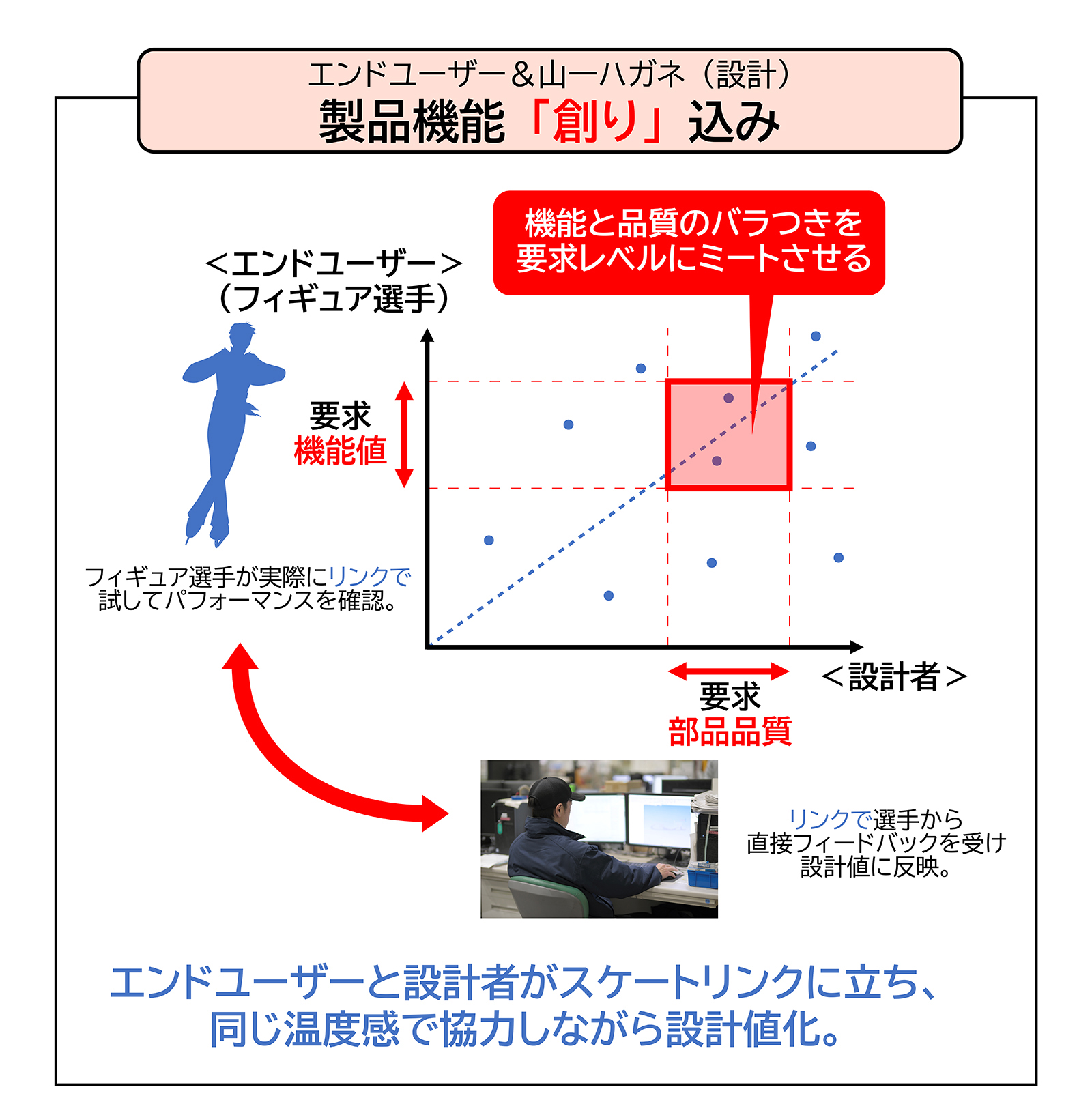

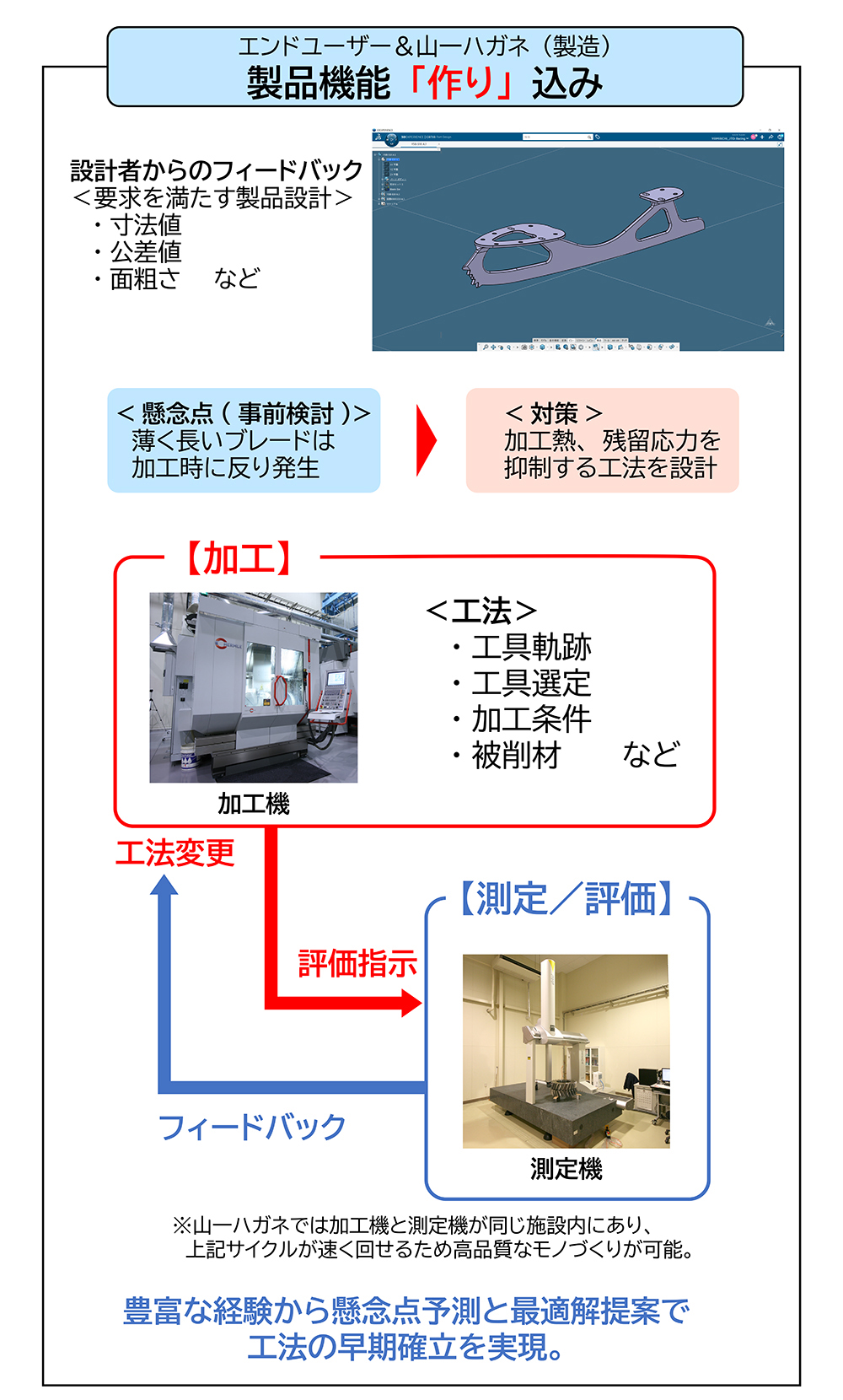
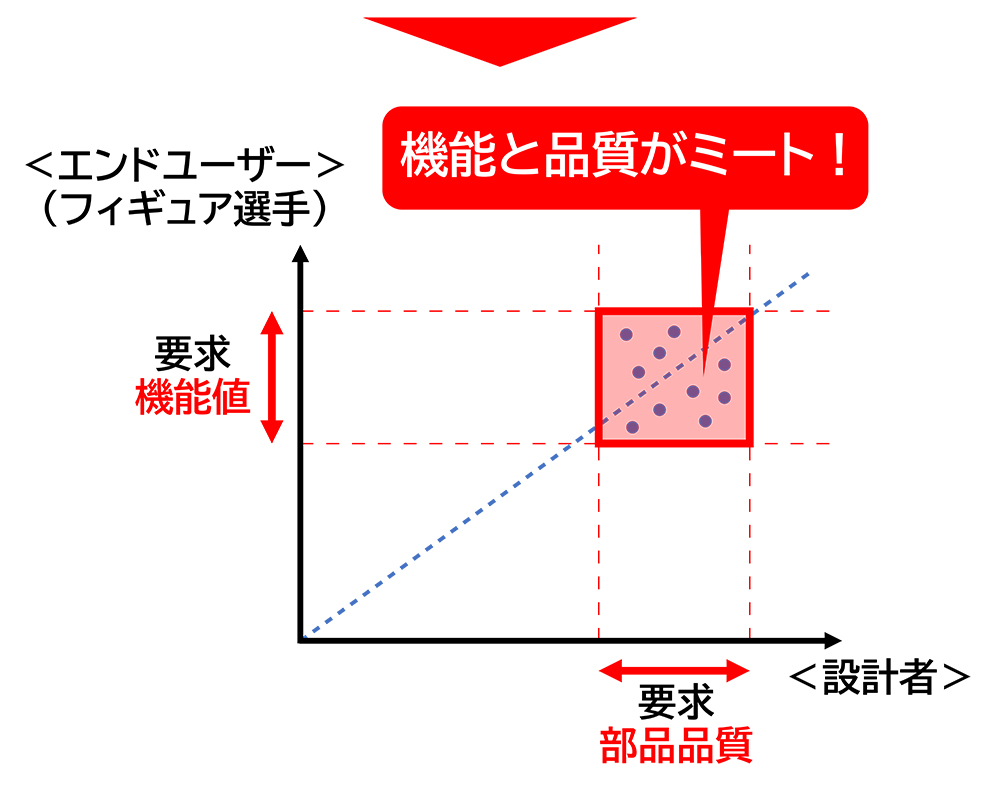
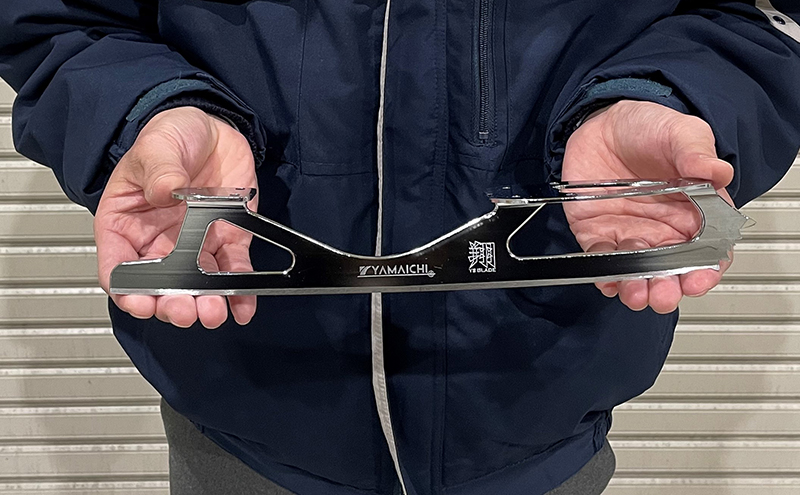
世界最高品質、世界唯一の削り出しブレードの量産を実現!
次々発生するエンドユーザーの要望や問題点も素早く解決しながら「進化」し続けている。
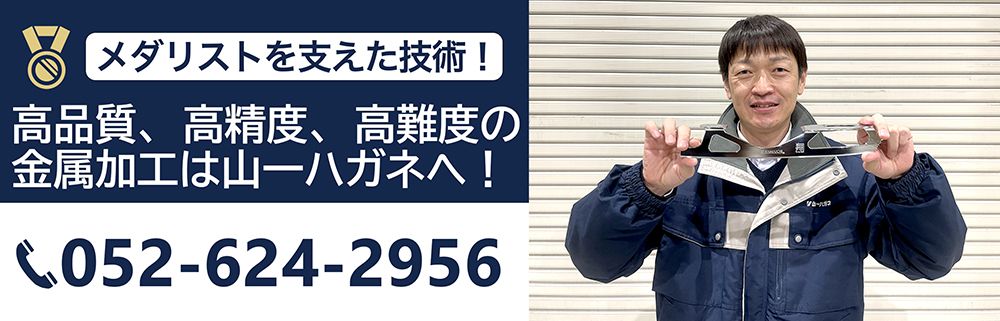