3Dプリンタ発祥の地・名古屋から未来へ。「縁」がつむぐ技術の系譜-3Dプリンタ発明者小玉秀男氏来社レポート-
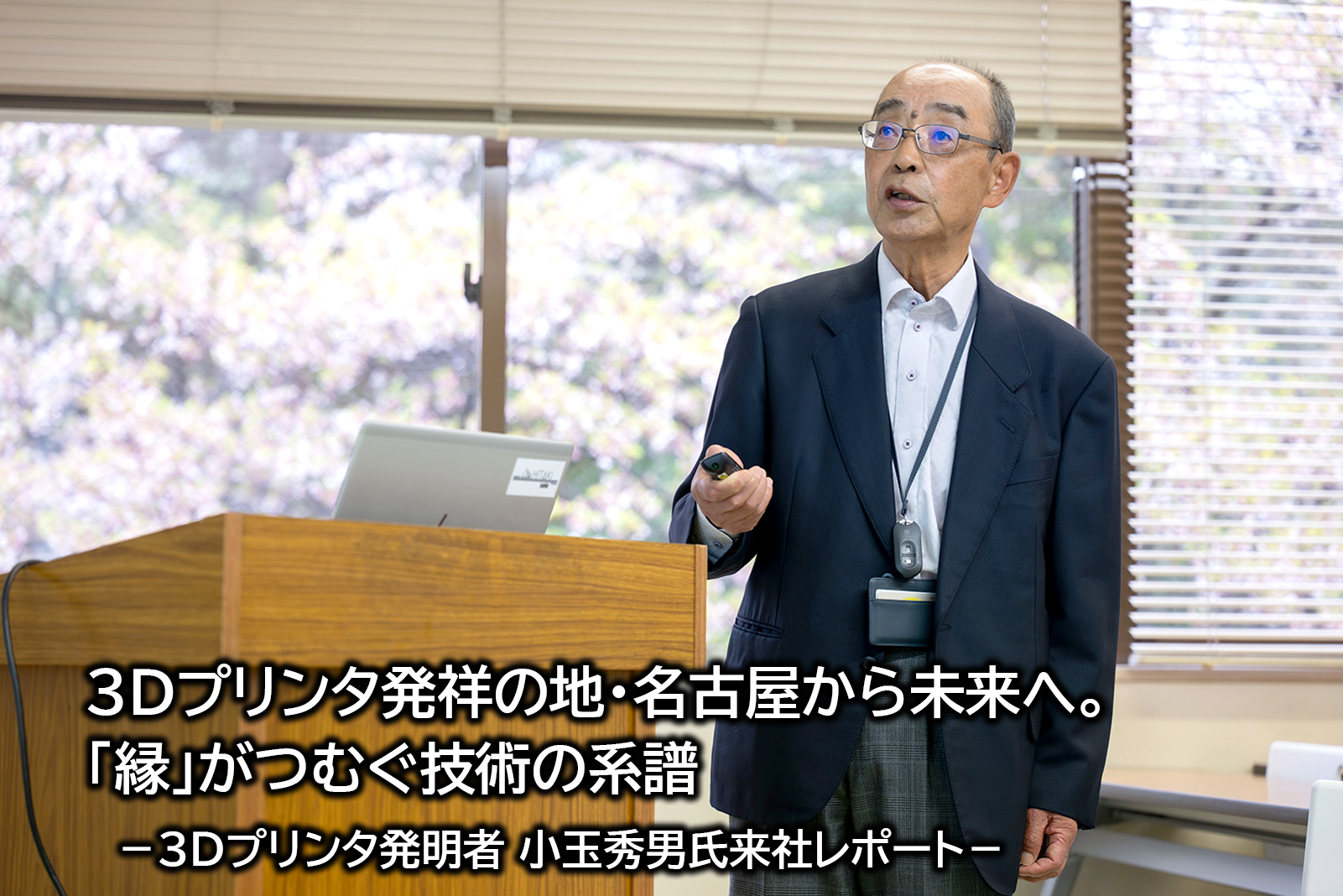
名古屋生まれの3Dプリンタ技術が名古屋で花開く
2025年4月10日。
名古屋市緑区の山一ハガネの本社に、3Dプリンタ発明者として知られる小玉秀男氏が訪れた。
今回の訪問は、ある技術の“縁”がきっかけだった。
山一ハガネは、令和6年度 名古屋市工業研究所主催の『名古屋市工業技術グランプリ』で名古屋市工業研究所長賞を受賞。
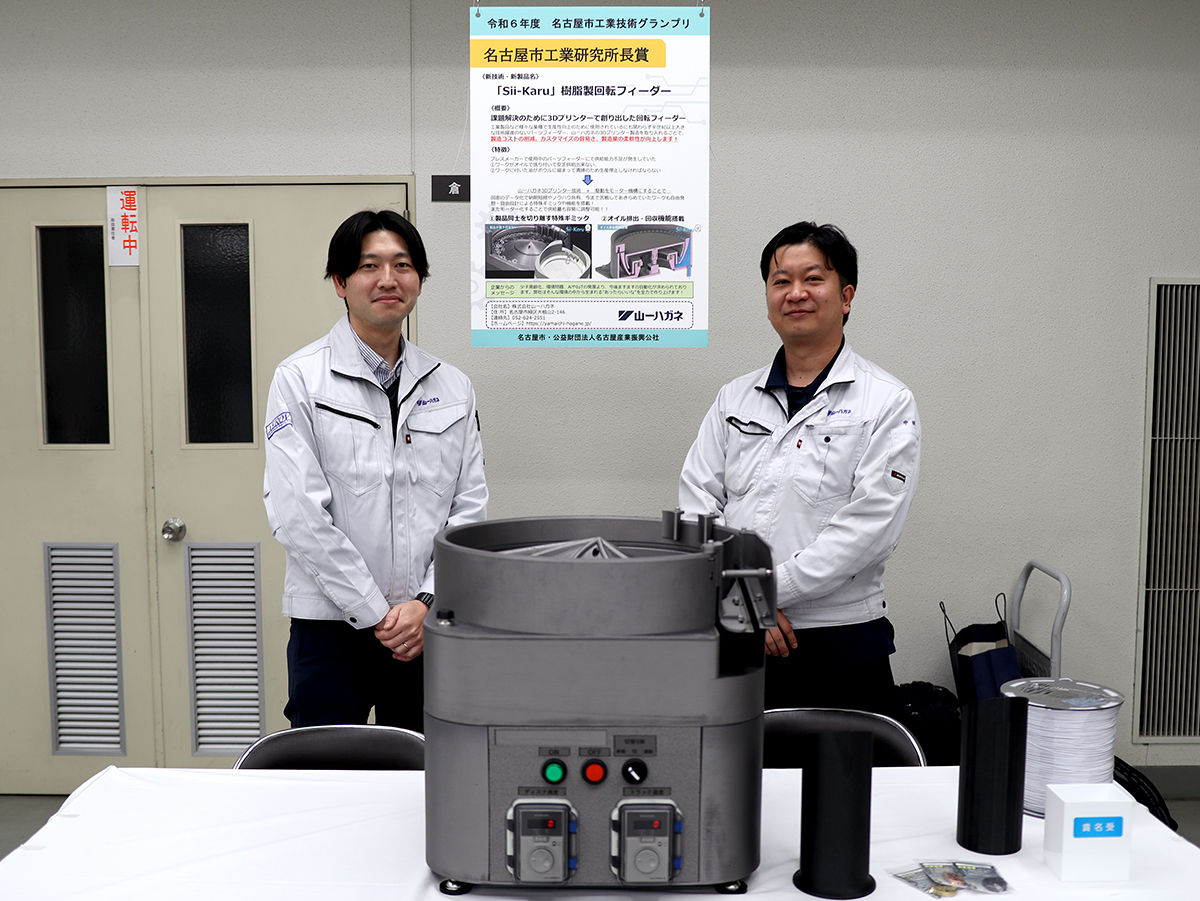
研究所長賞を受賞した樹脂3Dプリンタ製回転フィーダー『Sii-Karu』
小玉氏は約45年前、名古屋市工業研究所に在籍、そこで「立体図形作成装置」の特許を出願し、世界初の3Dプリンタ技術を発明した。
その技術が、今、同じ名古屋の企業により現場で機能する実用技術として磨き上げられ、モノづくりの現場で活かされている。
この偶然とは思えない“縁”に強く惹かれ、弊社より小玉氏に来社を招聘申し上げたところ快諾いただき、今回の訪問が実現した。
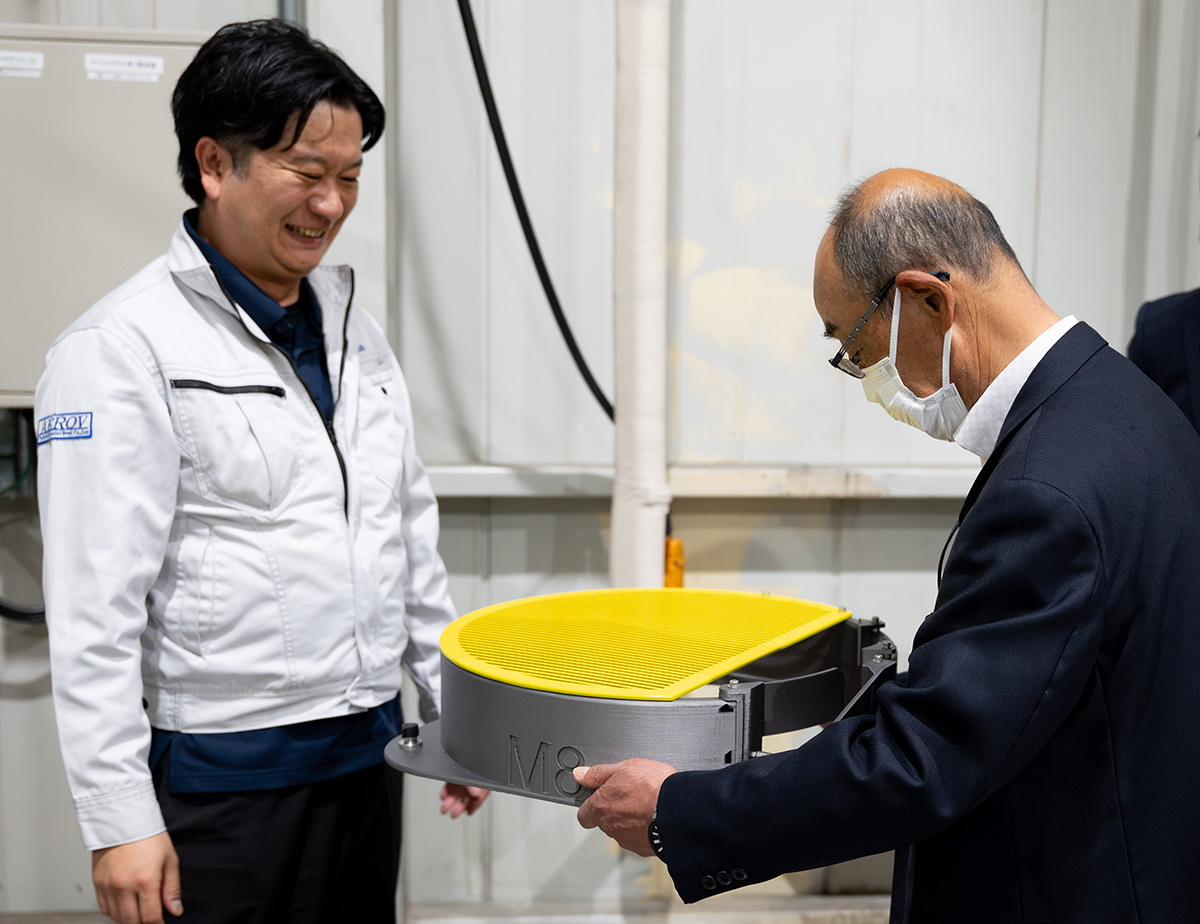
3Dプリンタで作られたSii-Karuの部品を興味深そうに見る小玉氏
山一ハガネの自社製3Dプリンタ『3IxD(スリーイクシット)』開発の舞台裏
山一ハガネが3Dプリンタに取り組み始めたのは、およそ10年前。
金属製3Dプリンタでの航空機部品製造に携わる中で、ある違和感があった。
「最先端の技術、設備を導入しているのに、現場で活用しきれていない。」
当時、導入した海外製の金属3Dプリンタは、たしかに精度は高かった。
しかし、その代償として操作性に難があり、また、造形ミスも目立った。
プリンタが止まれば現場も止まる。
想定通りに動かないプリンタに、山一ハガネの技術者たちはもどかしさを募らせていた。
そして、業を煮やし「それなら、自分たちで作ってしまおう!」と考え、自社製3Dプリンタ『3IxD』の開発がスタート。
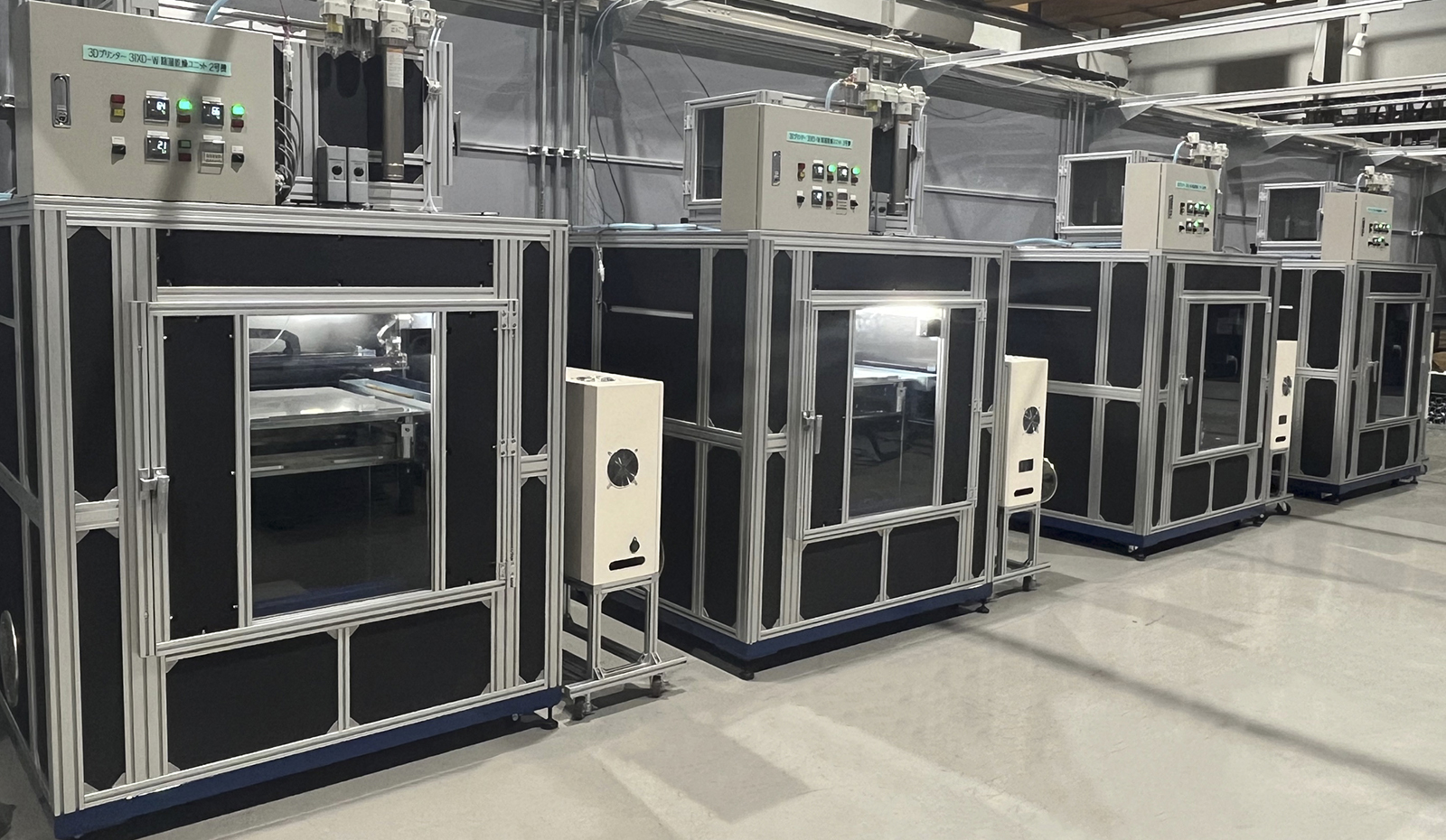
山一ハガネ製3Dプリンタ『3IxD』
技術者たちは“作りたいモノに合わせてプリンタを仕上げる”という逆転の発想で開発に取り組んだ。市販の3Dプリンタのように、装置の性能に人が“合わせる”のではない。用途や製品に応じて、プリンタのほうを作り変えていくというアプローチだった。
また、素材は金属ではなく樹脂に切り替えた。理由はシンプルで日本の樹脂技術は精密さと耐久性に優れているからだ。。
金属3Dプリンタに比べ、装置の自由度も高く、応用の幅も広がると判断。
製品づくりの視点から逆算し、樹脂を選び、プリンタの設計を突き詰め、制御ソフトウェアも独自で開発。山一ハガネの3Dプリンタは、完全に自社製になった。
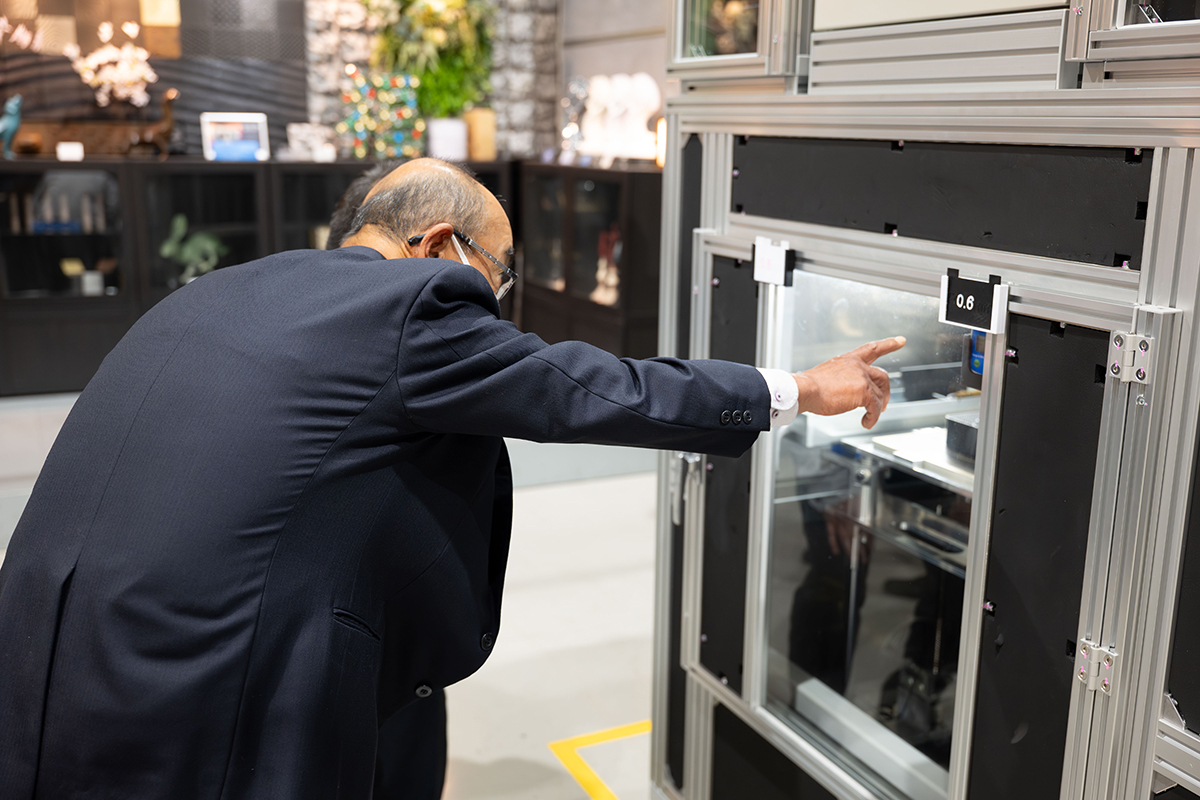
自らが発明した技術の現在を見る小玉氏
「形が分からなかった」…発明の原点は“困りごと”から
今回、小玉氏に山一ハガネ本社で『XYZプロッタの創成期顛末』というテーマで講演いただいた。
「きっかけは、そもそも自分が分からなかったからなんです。」
1970年代後半、小玉氏は名古屋市工業研究所在籍時に、当時の最先端技術であった3D CADに出会った。
当時の3Dデータは、コンピュータ画面の中で存在していても、その形がどうなっているのか説明できなかった。
「これが円なのか球なのか、立方体なのかすら分からない。説明しようにも伝わらない。」
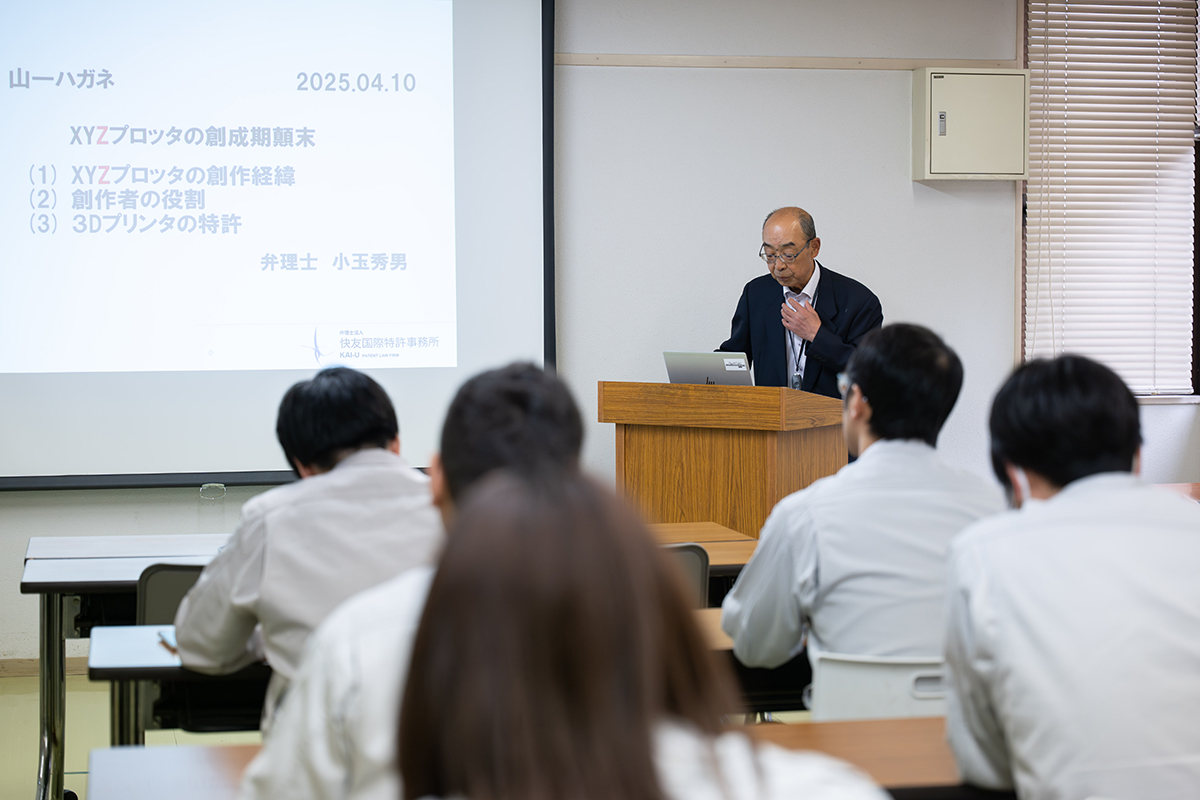
技術者を前に講演を行っていただいた
その不便さが、3Dプリンタ技術発明の原点だった。
そんなとき、ある印刷技術の展示会で見たのが『版下作成装置』だった。
紫外線を当てると硬化する感光性樹脂に、マスクフィルムを重ねて光を照射する。つまり、光で形を描くという発想。その技術に、何か可能性の種のようなものを感じたという。
「これ、もし層を重ねていったら、立体になるんじゃないか?」
そう閃いたのは、展示会場を出て岐路につくバスの中でのことだった。
積層の閃きと『XYZプロッタ』誕生の瞬間
そこで、まず着手したのは、マスクフィルム方式での試作だった。
1層ずつ紫外線で硬化させたフィルムを重ね、建物のミニチュア模型のようなものを作る。
部品は自作。光源の制御、マスクの調整、積層のズレを防ぐための工夫…すべてが手探りの中で行われたという。
その努力の末、完成した試作は27層で構成された『家の模型』だった。
今でこそ、家庭用3Dプリンタでも簡単に出力できるものかもしれない。だが当時、それを立体造形で再現するという発想は、世界中のどこにもなかった。
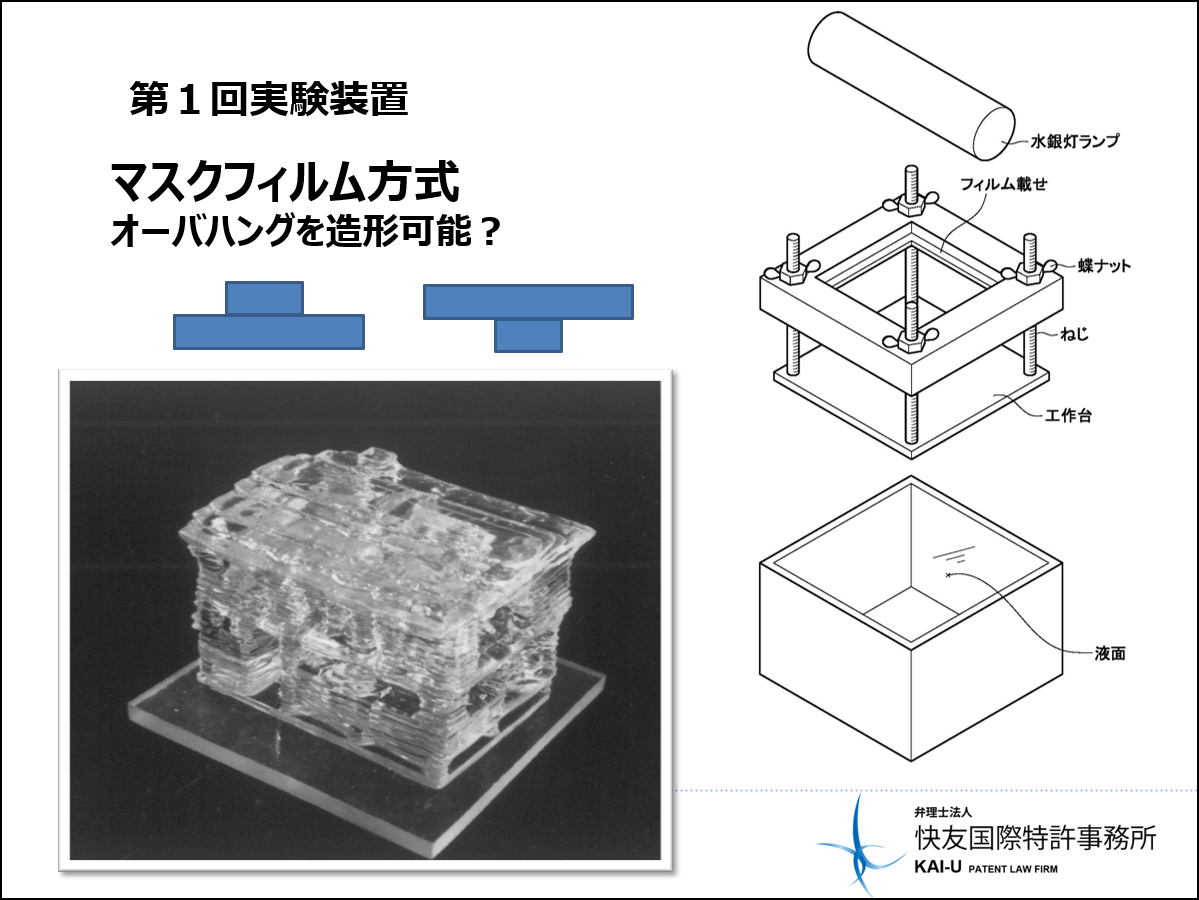
世界初の立体造形モデル(小玉氏の講演資料より)
さらに次に取り組んだのが、マスクレス方式の実験。
マスクを用いず、紫外線を照射する光源そのものをX軸・Y軸方向に動かすことで、任意の形状を直接描く方法だった。
「X軸、Y軸に加えて、層を積むためのZ軸を組み合わせれば、3次元空間に線を引けるようになるんです。」
この発想こそが『XYZプロッタ=3Dプリンタ』のコンセプトへとつながっていく。
当時はまだ、2次元図形を描くXYプロッタがようやく登場し始めた頃だった。そんな時代に、小玉氏はZ軸=高さの概念を加え、空間の中に“形”を描く機械という概念を考えたのだ。

マスクレス方式に進化し3Dプリンタの原理を確立(小玉氏の講演資料より)
「形を描くのではなく“出す”。それができたとき、これはいけると思ったのです。」
その発想が当時の技術の常識の中でどれほど画期的だったかは、今振り返っても驚かされる。
早すぎた技術と、特許の4つの教訓
XYZプロッタとして技術の輪郭が固まり、試作品ができ、原理が確信へと変わった頃、小玉氏は論文を書き発表した。
「これは面白い!」「これが未来だ!」そんな反応を期待していたが、周囲の反応は想像と違ったものだったという。
理解されなかった理由のひとつは、当時 “形を出力する”という概念がなかったからだ。
設計図は二次元、製造は職人、試作品は模型屋。
データから直接“形”を出すという発想は、あまりに時代が早すぎた。
「当時は誰からも評価してもらえませんでした。でも、色々と後悔もあります。」
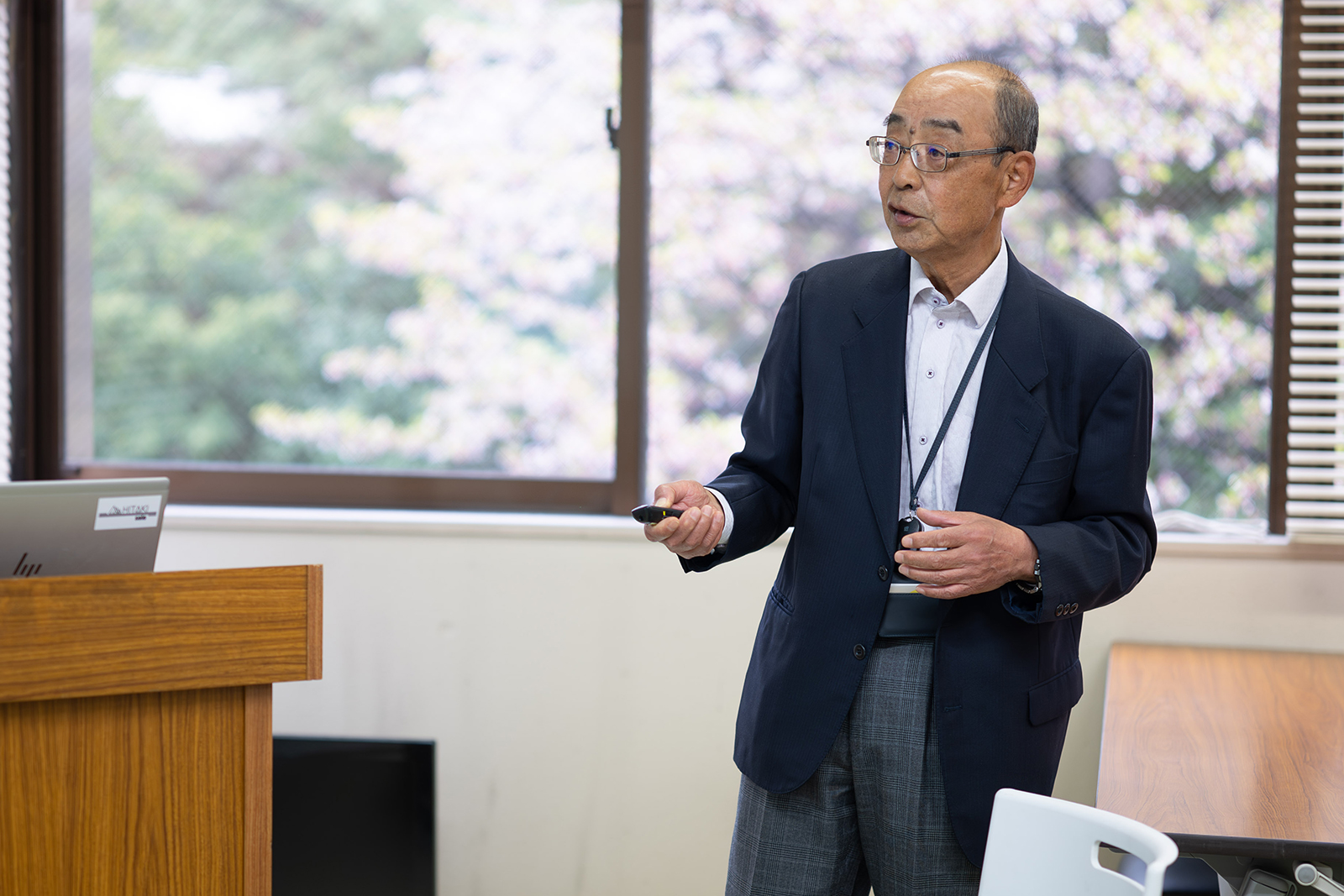
自らの経験を元に技術者たちへ思いを語る
小玉氏によると、特許出願時に以下の4つの反省があったという。
- 外国出願をしなかったこと
- 審査請求を忘れ、権利が消滅してしまったこと
- 関連技術を出願しなかったために、他社に特許を取られてしまったこと
- 弁理士に頼らず、全て自力で処理してしまったこと
いずれも、当時の知財制度を知らなければ誰でも陥りかねない落とし穴だった。
しかし、それを正直に振り返り、行動に移すことの重要性を語る。
「やはり、実際にやってみることが大事だと気付かされました。『これも同じでしょう』と決めつけてしまわず、頭の中にあるものは一度、実際に形にしてみる。そうして初めて、違いや気付きが見えてくることも多いんです。」
講演のなかで、小玉氏は創作者の役割についても語った。
それは、技術を見せびらかすことでも、理論を誇示することでもない。
「創作者には、技術を必要とする人に応える責務があるのではないでしょうか。たとえば、臓器や骨のモデルを造形することで、医師が手術の事前検討を行えるようになるように。
多くの人は、そうした技術の存在すら知らない。だからこそ、創作者にしか見えていない世界を、社会にどう伝えるかが問われているのです。」
その言葉は、まさに今、技術を現場に届けている山一ハガネの技術者たちにも、深く響くものとなった。
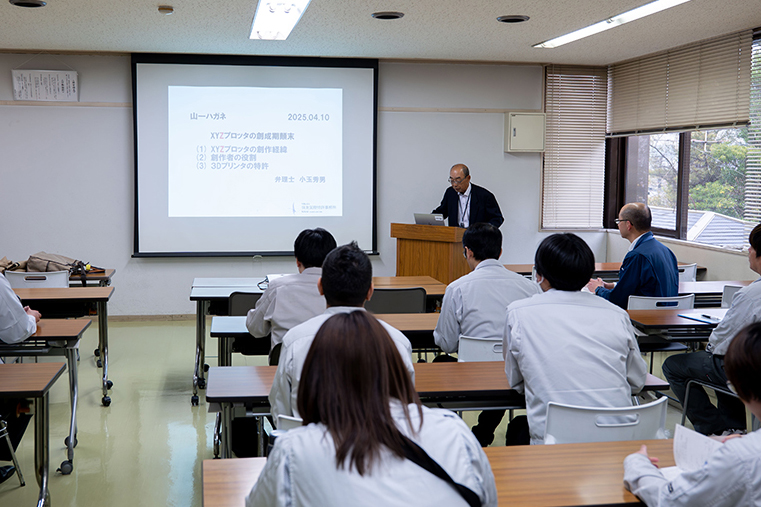
真剣に講演を聞く山一ハガネの技術者たち
考え続けることの大切さと発明者の哲学
「私は、割と好きなことはずっと考え続けています。頭の中のどこかに常にあるのでしょうね。そうしていると、電車に乗っている間に気が付いたりすることもあります。」
小玉氏は、幼少の頃から好奇心が旺盛で「なぜ?」「どうして?」を繰り返してきたという。
問いを持ち続けることが、小玉氏にとっては日常だった。
「何かを思いついたときに忘れないように、ノートの付け方には工夫していました。ずっと考え続けるための仕組みを持っておくことが大事なのです。」
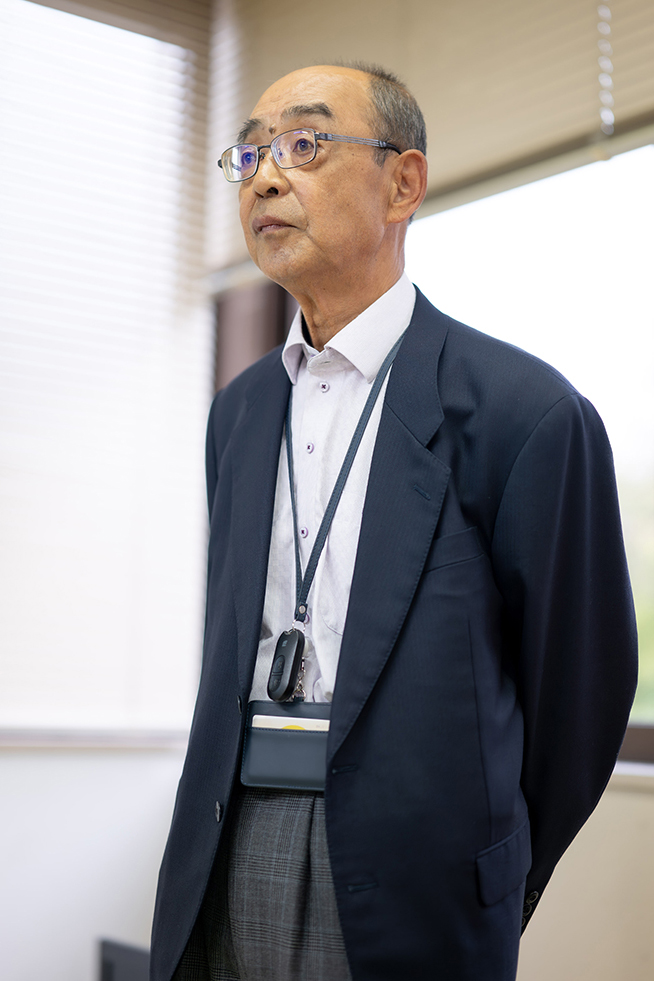
ずっと考え続けることが大事と語る
どこまでも実直で、どこまでも等身大。
小玉氏の思考の根っこには、常に“自分ごと”としての課題意識がある。
派手な成果よりも日々の疑問を大切にすること、向き合い続けること。
「不便だなって思って、それを何とかしようと考える。で、ふと『あ、これだ』と気が付く瞬間が来る。そのためにずっと考え続けることが技術を生むのだと思います。」
発明者が見た、山一ハガネの3Dプリンタ技術の現在地
山一ハガネの現場を見学した小玉氏は、想像を超える完成度に驚きを隠さなかった。
「ここまでしっかりした製品ができているとは、正直、夢にも思いませんでした。」
3Dプリンタでつくられた分別機や、回転構造をもつパーツ。
それらは見た目の精度だけでなく、実際にネジが回るほどの耐久性を持っていた。
『おもちゃ』や『試作品』というレベルではなく、現場で使われていることがすぐにわかる品質だった。
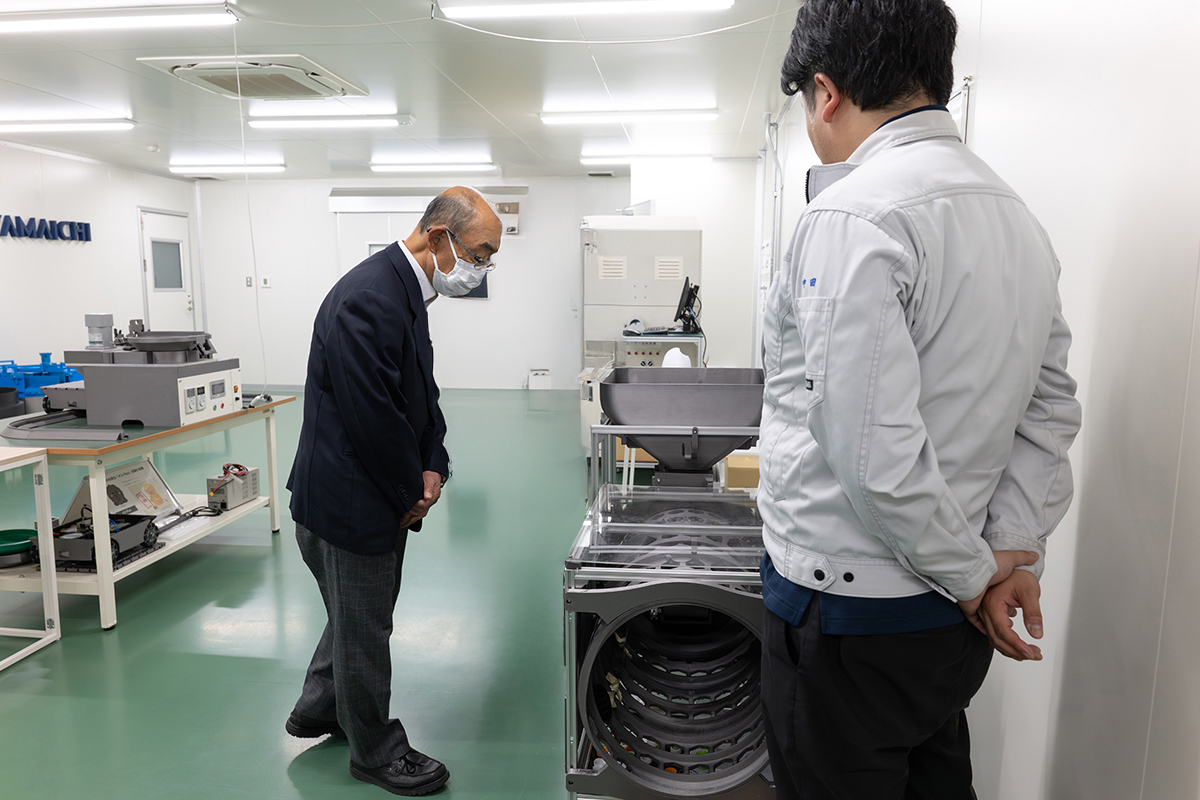
実用に耐える3Dプリンタ製品に驚く小玉氏
「これまで、いくつもの3Dプリンタ製品を見てきましたが、ここまで実用に耐えるものは、なかなかお目にかかれないです。」
と、小玉氏は製品を手に取りながら感心した様子だった。また、発明当時のことを振り返りながら、次のように語る。
「私は『これがあれば形にできるんじゃないか』という発想からスタートしました。自分が困っていたからこそ、『こういうものが必要なんだ』と自然に思えたのです。」
目的があって、そこに合わせて技術の方を組み上げていく。
それは、山一ハガネの現場で実践されている“お客様の課題から逆算したモノづくり”と、小玉氏がかつて取り組んでいた“課題起点の技術構想”とが、重なる部分だった。
技術を押しつけるのではなく、必要な人に、必要なカタチで届ける。
小玉氏が目指していた創作者の責務が、ここにしっかり息づいていた。

3Dプリンタは“必要なカタチ”に応えるために発明された
未来へ。“つながる”3Dプリンタ技術
名古屋市工業研究所在籍当時に小玉氏が発明した『立体図形作成装置』。
その発想と構想は45年の時を超え、同じ名古屋の企業である山一ハガネの手により“モノづくりの現場でお役に立つ技術”として、まさに今、花開いている。
今回の来社は、技術を見ていただくだけではなく、技術の過去と現在、そして未来を語り合う場でもあった。
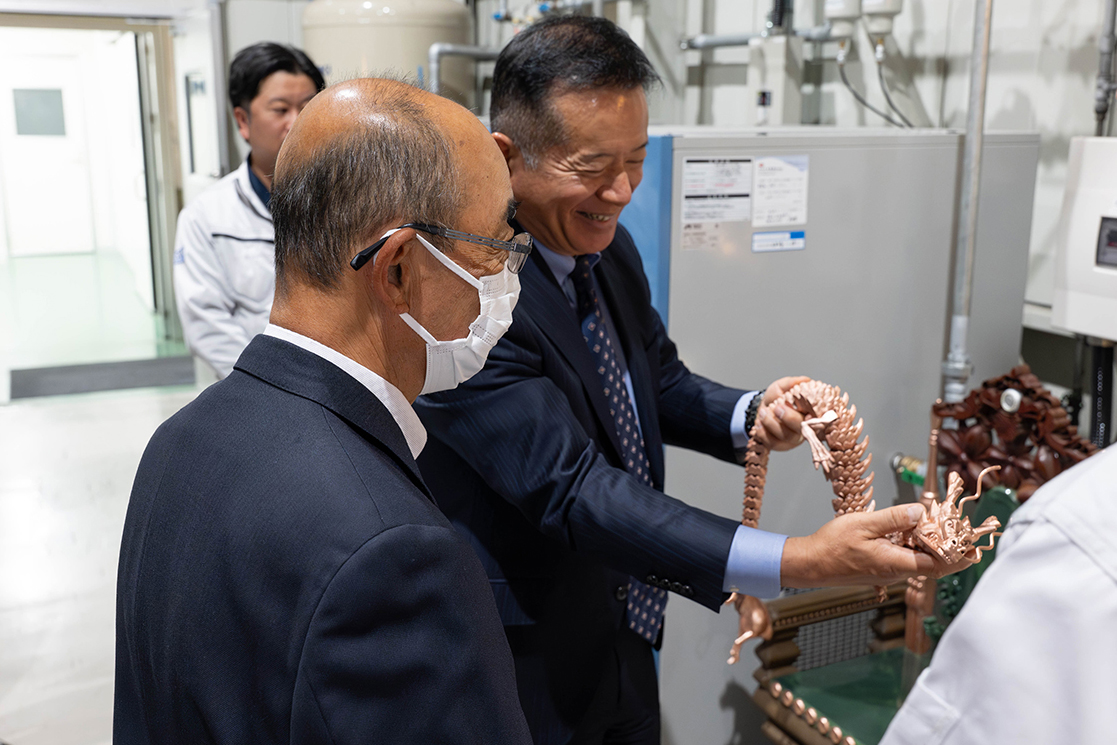
小玉氏と笑顔で語り合う山一ハガネ代表取締役 寺西(右)
「現場でちゃんと使われているというのが、やっぱり嬉しいですね。」
小玉氏は、発明当時の想いが現場で生かされていることに深く頷く。
その姿からは、受け継がれた技術が動き出しているという実感が滲む。
実際に、山一ハガネの3Dプリンタ技術は、現場の課題解決に力を発揮し始めている。
たとえば、バレル研磨の現場において、研磨後の製品と研磨石を分別する工程で、従来2人1組・1日5回・1回2時間という工数がかかっていたが、山一ハガネが開発した樹脂製ドラムフィーダー『Karudora』の導入により、分別作業の全自動化を実現。分別精度100%、作業負担の大幅軽減という成果を上げている。
☞3Dプリンタ製ドラムフィーダー『Karudora』導入事例
こうした実績は、同様の課題を抱える現場にとっても、新たな解決手段となり得る。
一方で、3Dプリンタ技術が実用段階にあることの、何よりの証でもある。
そして今後は、この技術をさらに多くの現場へ届けていくために、他の企業や技術を通じて共創できるパートナーとの新たな連携を進めている。
「必要だからつくる。」
3Dプリンタ発祥の地・名古屋から未来へ。受け継がれたバトンが新たなカタチを描き出す。
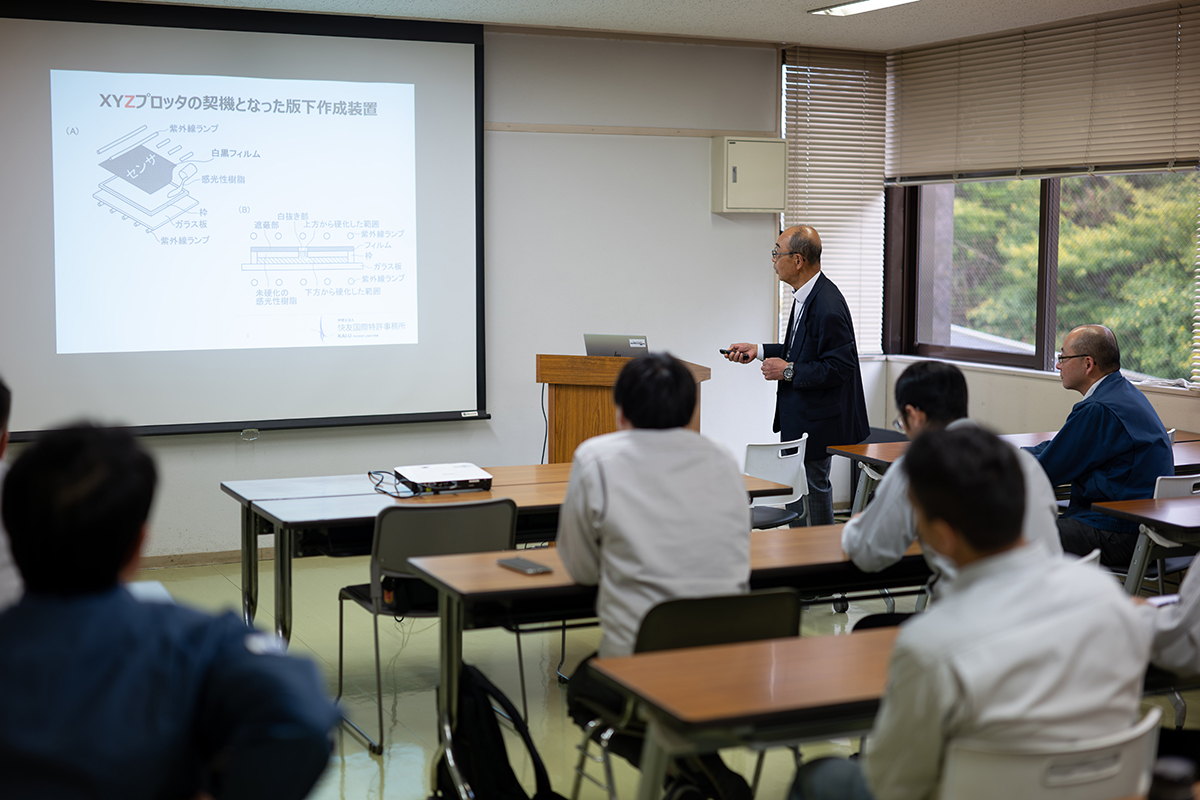
技術者としての原点ともいえる想いが、次の世代へ受け継がれていく
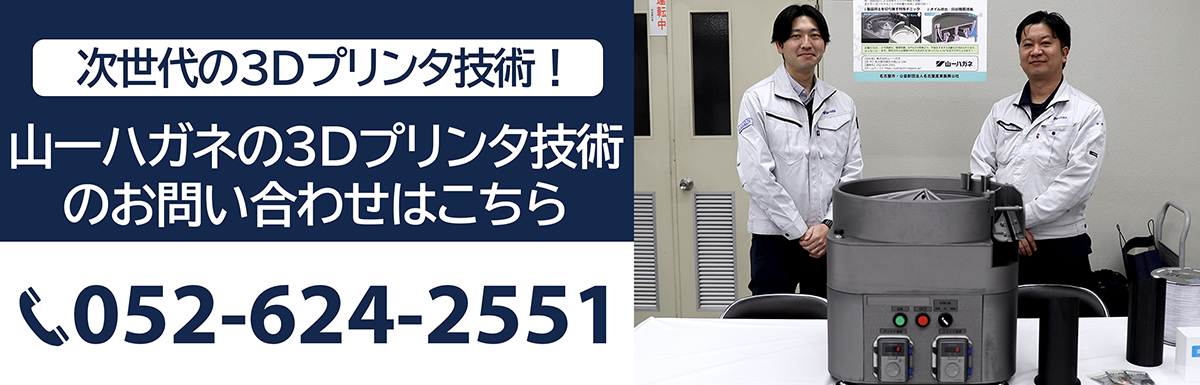