なぜハガネ屋がAM(Additive Manufacturing)事業?!
———目指すのはファクトリーモールを超える究極の『ネオ ファクトリーモール』
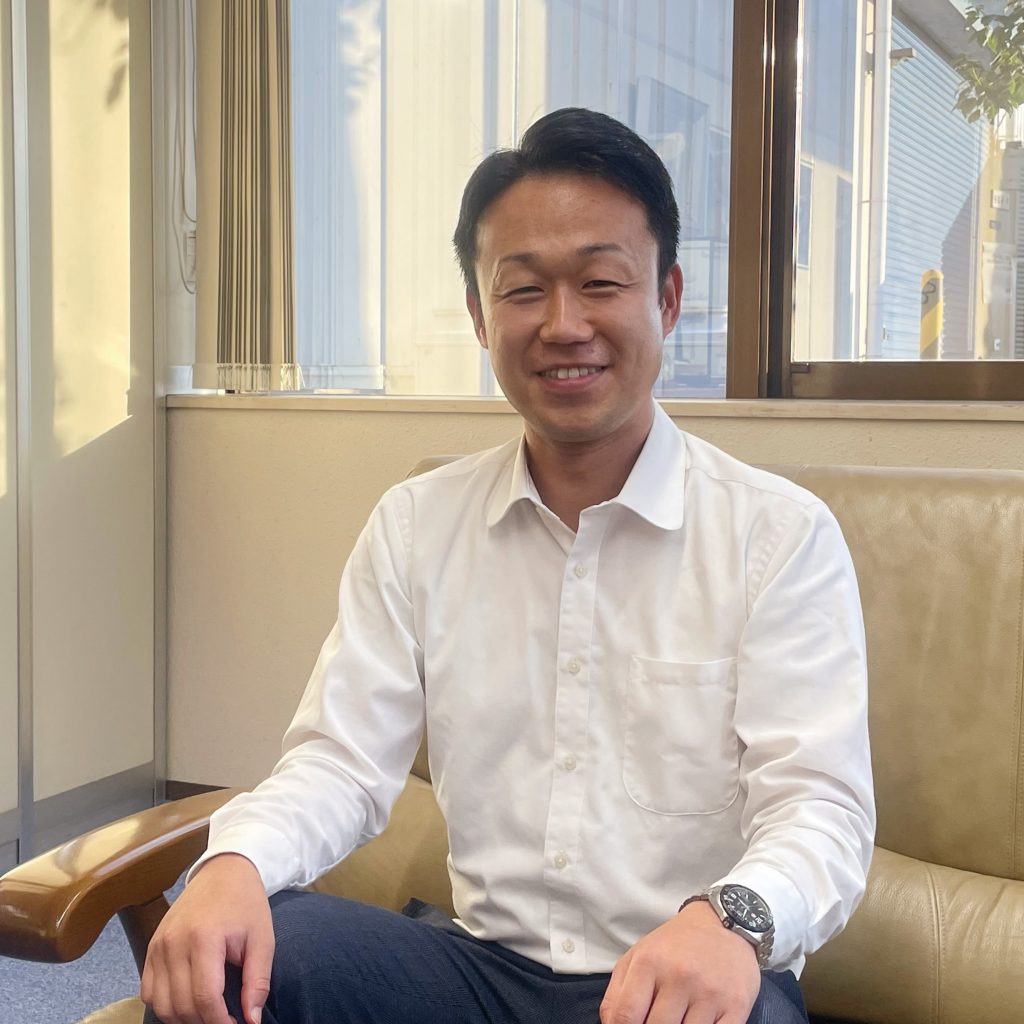
株式会社山一ハガネ
事業開発Sec. マネージャー
小林 祐太
■時代の変化に対応し続ける山一ハガネ
創業時から特殊鋼のプロとして自動車などの量産品の製造業を支え、共に成長してきた山一ハガネ。
しかし、インターネットの普及やIoT、AIの発展・活用により顧客のニーズが高度かつ多様化した。そのニーズに応えるべく製品の製造技術もすさまじい勢いで進化し、従来の大量生産やオーダーメイドだけでなく、少ない数量での一品一様化に対応できるような時代になってきた。
大量生産、オーダーメイド、そのどちらでもないのが多品種少量生産(マスカスタマイゼーション)だ。
性能やデザインなどを顧客のニーズに合わせて個別にカスタマイズして製造できるAM技術への期待は近年ますます大きくなっている。そして、様々な製品・部品が多品種少量生産されるようになるとそれらに適したバリエーション豊かな治具をスピーディに、効率よく準備する必要性も生じてくる。
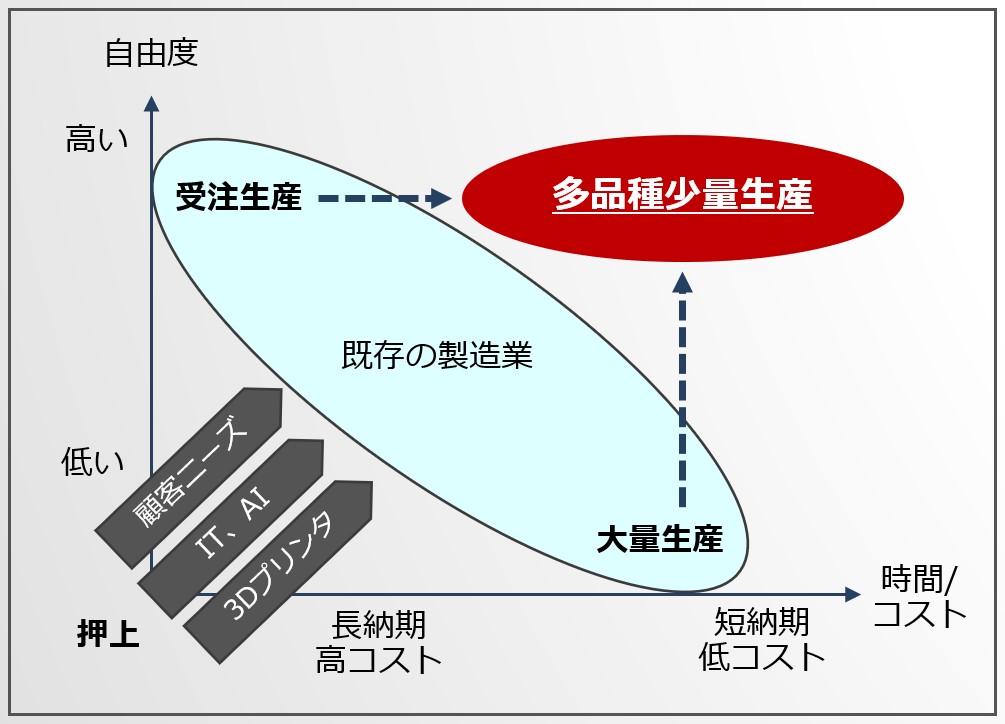
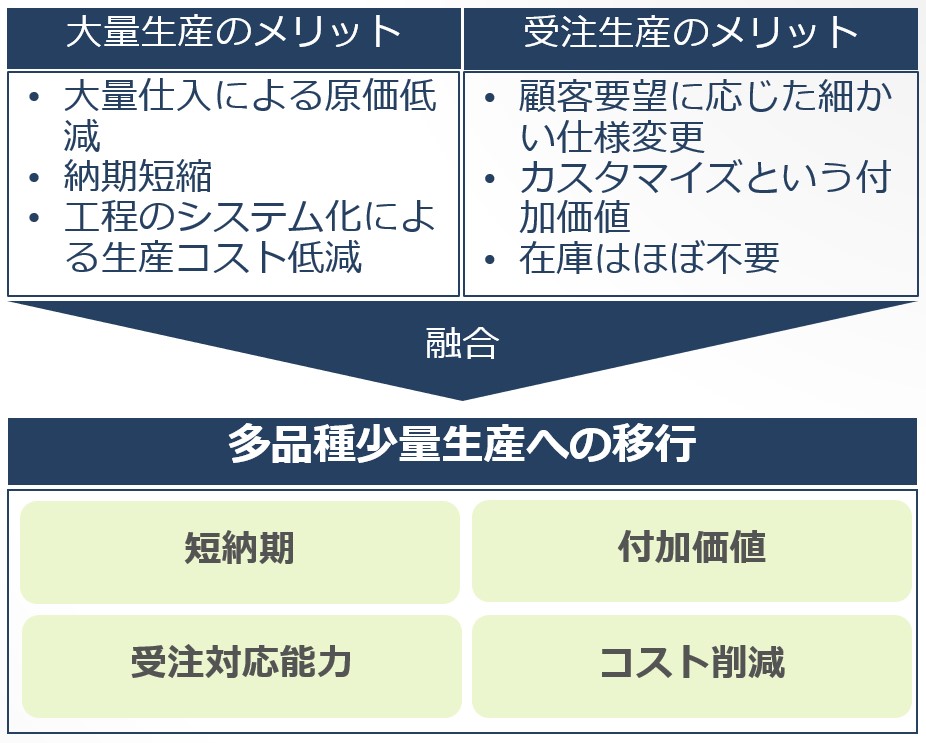
これまで量産品を支えてきた山一ハガネは、その多品種少量生産に対し、AM事業で新たなカスタマーファーストを。
こうした未来を見据え、山一ハガネのAM事業化計画は2016年から始まっていた。切削機械が並ぶ広い工場に3Dプリンターや塗装機・レーザー設備を導入。
お客様のニーズに、ハガネとAMの両輪で応えていくため、練りに練った大計画のスタートであった。
■周知されていかないAM技術
消費者ニーズの多様化に対応すべく、AM事業へ参画した山一ハガネ。しかし、その道のりは簡単ではなかった。
山一ハガネのAM事業部は2016年からスタートしている。しかし、現在も日本国内では“Additive Manufacturing”というものがほとんど周知されていない状態だ。日本人のイメージでは“Additive Manufacturing=3Dプリンター”というイメージで、3Dプリンターは試作や開発用といった印象が強いのではないだろうか。
海外では、3Dプリンター=ホビー、Additive Manufacturing=工業という認識である。
しかも、ハガネ屋がAM事業をやりだしたのだから当然、実績など何一つない。日本人の文化として実績のないものは導入したがらない風潮が強く、周知されていくには厳しいものがあった。
6年もの間、国内外の企業や大学などと研究・開発を行い、3Dプリンターの造形時の診断ができる自社製ソフトウェアの開発など、地道な努力によって実績を積み重ねることで、山一ハガネのAM事業を周知させていったのだ。
■ファクトリーモールが支えるモノづくり
山一ハガネは創業当時から特殊鋼を取り扱い続け、現在では材料から加工・品質保証・出荷まですべてを自社で行う製造体制を構築しており、特殊鋼の“ファクトリーモール”となっている。
そしてそのファクトリーモールという精神はAM事業でも変わらない。
マテリアル(材料)では、3Dプリンター用フィラメントの開発から製造、販売を行い、デザイン(設計)では構造の最適化ができるソフトウェア“nTopology”をエンジニアが熟知している。
さらに、プリンティング(造形)は温度と湿度をコントロールすることで、より精度の高い製品を作り出せる自社製3Dプリンターを開発し、ポストプロセス(後工程)では塗装・レーザーによって高い付加価値を付与することができる。
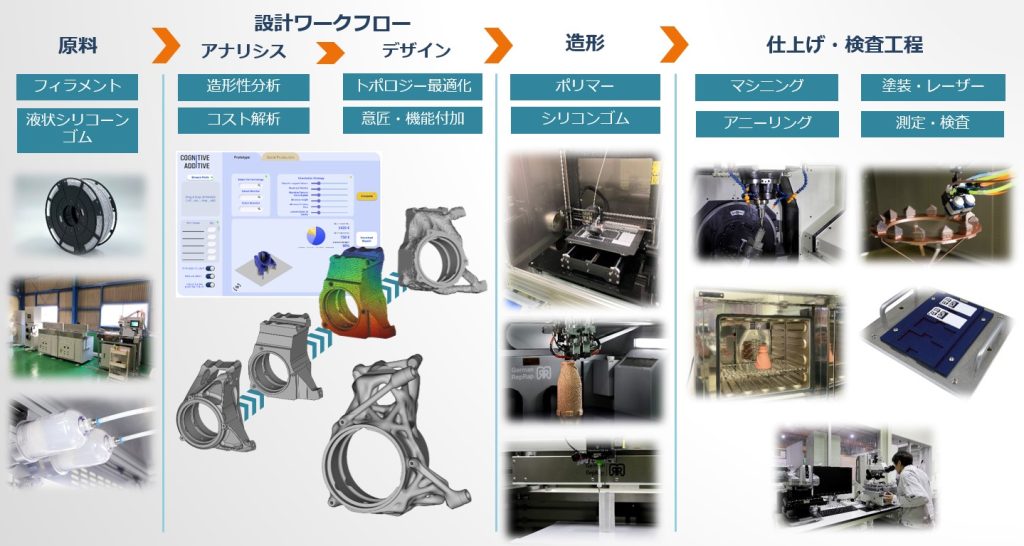
「マテリアル(材料)」「デザイン(設計)」「プリンティング(造形)」「ポストプロセス(後工程)」これら4つのすべてを自社で行えるような企業は全国、いや世界で探しても山一ハガネ以外にはない。
また、設計を担うエンジニアとも密な打ち合わせが可能なため、細かな要望を直接伝えることができ、ニーズにぴったりと合ったモノづくりが実現する。
さらに、仕上げのためのポストプロセス(後工程)の段階では、マシニング、レーザー、塗装、それぞれに自身の技術を世界一と自負する技術者たちがモノづくりを支えている。
山一ハガネのモノづくりに妥協は一切ない。
■金属から樹脂へ。材料の置き換わり
私たちの身の回りや工場などには、金属でできた物で溢れている。自動車の部品や、食品加工を行う工場では規格外のものを吹き飛ばすためのエアノズルなど…。
それらは昔から金属で作られているために、「金属製で当たり前」のものとして存在している。
工場で使用する製品の多くは、細かいニーズに応えるために職人の手作業による特注だが、しかしそれには、設計変更への柔軟な対応が難しかったり、金属材料の部品点数が多いことで治具の重量が増加し、作業性や安全面での課題があったりする。
それらが今、これまでの金属製のモノづくりから続々と樹脂製に移り変わっている。
大きな理由としては、やはり軽量化である。アルミ合金と樹脂の比重を単純に比較すると1/2の重さだ。
さらに、樹脂はさまざまな化学元素を添加することにより、硬さや耐熱性を付与するなど特性の異なる材料を作ることも可能なうえ、金属よりも低コストなのだ。
先述したように金属より樹脂の方が軽く、既存のものよりも軽量化が可能なため、自動車や航空機の部品に使用されれば燃費向上が実現したり、工場の設備や治具などに採用されれば、体力や筋力の少ない人でも現場で活躍する幅が増えたりもする。
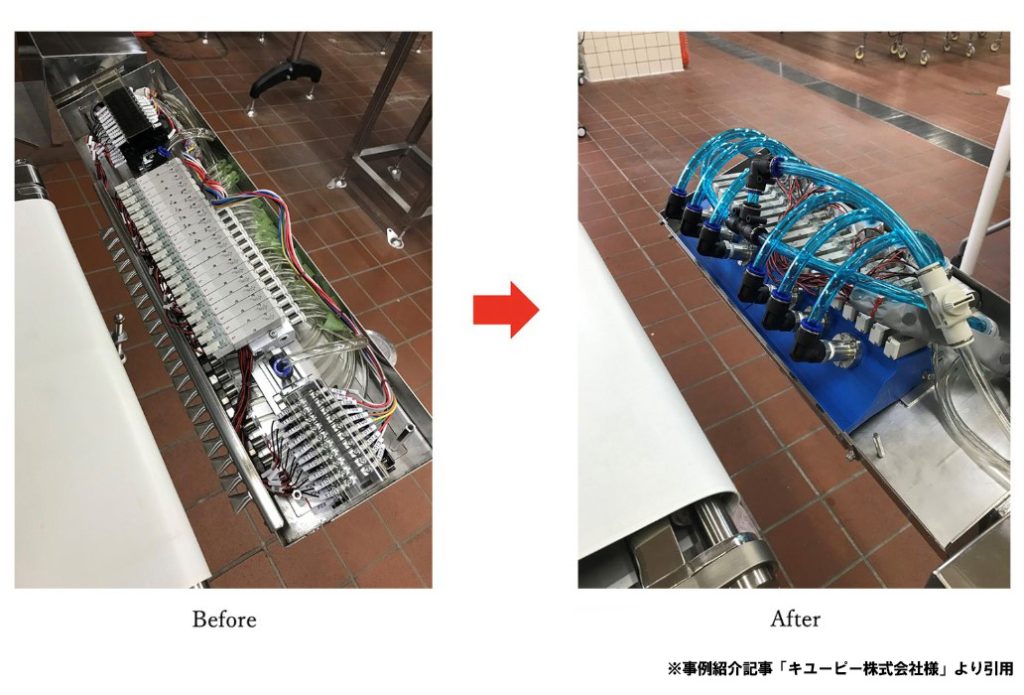
何年も前から日本にも3Dプリンターによる樹脂成型の技術があったにもかかわらず、なかなか金属から移り変わらなかった原因は、金属が扱いやすかったのもあるが、やはり強度面で金属の方が優れていたからだ。
しかし、nTopologyのような、形状を最適化することのできる設計ソフトが出てきたことによる強度面を考慮した設計や、CognitiveAdditiveのような造形の診断ツールを用いることで造形時の扱いの弱点を克服。
だからこそ山一ハガネは材料から設計・造形・仕上げまで、AMのすべてを自社で手掛けるのだ。
■山一ハガネが描く今後のVISION
先述したように、山一ハガネはAM事業でも材料から仕上げまですべてを一貫して自社で行う、ファクトリーモールだ。
小林が思い描く山一ハガネのAM事業の今後のビジョンは、多くの人の課題やニーズを山一ハガネの持つAMワークフローによって解決し、少しでも多くの実績を生み出すことだ。
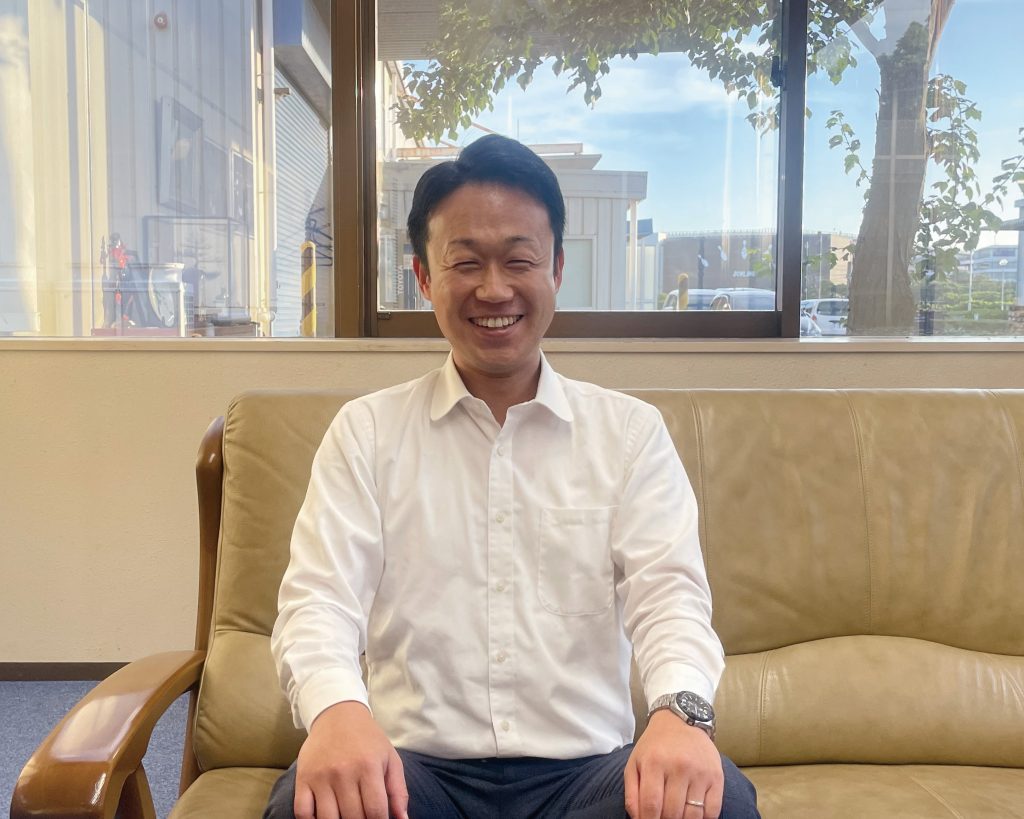
たとえば工場。何年も前から使っている特注で作られたような金属製品は、多少使い勝手が悪くとも現場の人の創意工夫でなんとかカバーしていたり、故障して再発注をすると高価であったり、手作業での作製のため品質にバラつきがあったりすることもあるのではないだろうか。
そんな場合も、山一ハガネのもつAM技術の活用によって、製品の作業効率をアップ。そして故障や仕様変更の際には同じ品質のものを金属より安価に、スピーディに入れ替えることができるようになる。
そのほかにも自動車、建築・インテリア、医療など、その現場で実際に働く人たちの要望を満たし、悩みを解決できるものが完成する。
素材の開発から設計、製造、仕上げ加工、販売・物流までを一貫して行える「ネオ ファクトリーモール」これが小林の目指す姿だ。
必要な量の生産を必要なタイミングで提供する。在庫を持たない、新しいモノづくりだ。しかも、既存顧客だけでなく一般顧客に向けた販売チャネルをもつ、究極のファクトリーモールである。
新しい時代に合った、新しいモノづくりを山一ハガネのAMワークフローが叶えていく。
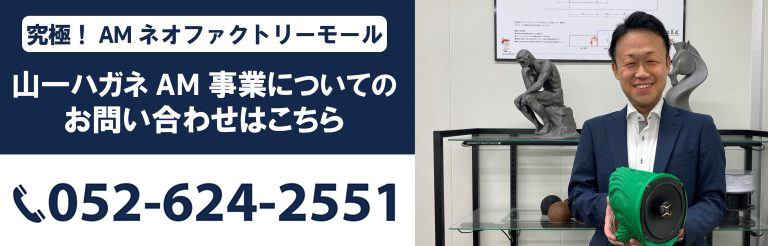